Serial vs. Parallel Robots: A Comprehensive Comparison Guide
What is a Parallel Robot vs. a Serial Robot?
These are designed to meet current industrial needs, and they've advanced motion control systems that promote precision and quality in the movement of goods. This new range of movement allows for such parallel robots vs serial robot to function over greater operating areas, thus offering flexibility in placement on the assembly line, but of course, flexibility in industrial applications as well.
Parallel Robots
Also known as a parallel manipulator, a parallel robot runs with multiple, independent kinematic chains that connect to a platform or end-effector. Parallel robots usually feature a static base and are known for high rigidity and relative accuracy. For example, the Delta robot acts as a parallel robot that's great for quick pick-and-place.
Serial Robots
A serial robot features one chain of connected joints, with the end-effector at the last joint. The most common form of a serial robot is the articulated arm found in industrial settings, such as welding and assembly; serial robots are known for their flexibility and ability to reach many different places.
Key Differences Between Parallel and Serial Robots
Kinematic Structure
• Parallel Robots: Multiple exist; there are multiple arms connected to the base and end-effector, which creates a kinematic structure that is more rigid and causes less deformation. Therefore, such structures maintain accuracy and stability with heavy loads.
• Serial Robots: Serial robots are more accurate in performance because of their ability to move based on design; thus, they are less accurate than parallel robots. They also do not manage heavier payloads well, as they use their joints to maneuver, which can be wobbly under heavy loads.
Degrees of Freedom (DOF)
• Parallel Robots: Due to their kinematic structure, parallel robots are more precise and have better end-effector positioning. Therefore, they're more likely to be found in use where precision is necessary, such as surgical robotics or robotic assembly. However, they may have decreased payload capabilities compared to serial robots.
• Serial Robots: Serial robots typically can manage a higher payload capacity but lack the precision of parallel robots. They are favored in industrial robotic arms or robotic welders because of their payload capacity.
Speed and Flexibility
- Parallel Robots: These are known for fast operation and are used in instances where speed and precision can happen at the same time, not to mention with pick-and-place. They are rigid and made for high-precision situations.
- Serial Robots: Serial robots may not be as fast in situations that parallel robots are, but they operate with flexibility, meaning they can be better used in situations that need more adaptability and range.
Precision and Payload
- Parallel Robots: Parallel robots have superior precision and end-effector positioning because of their construction. They allow for a tremendous level of precision for things like robotics for surgery or situations that require relying on robotic assembly. Their payload might not be as much as what serial robots could do.
- Serial Robots: Serial robots have a higher payload capability, although less precision than parallel robots. For things like welding or situations that require industrial robotic arms, serial robots are better.
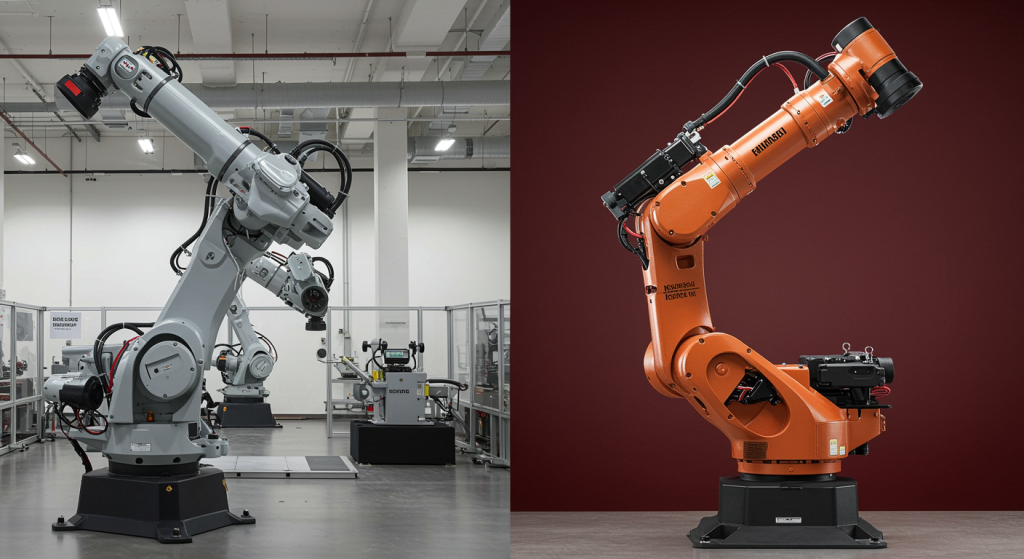
Advantages of Parallel Robots:
Precision:
Parallel robots are usually more precise in positioning. This is why they're found in 3D printing robotics, aerospace, and surgical robotics, to name a few.
Increased Speed:
Where speed is necessary—packaging or robotic assembly—serial robots cannot keep up with parallel versions.
Better in Confined Spaces:
Since parallel robots are more compact, they can be used in more confined spaces.
Decreased Kinematic Singularity:
They are susceptible to kinematic singularities that prevent them from functioning properly, and since serial robots are somewhat more malleable, they can operate for longer periods but also face more issues over time as they wear down.
Advantages of Serial Robots
Greater Range of Motion
Serial robots have a bigger work envelope and flexibility. That's why they are commonly used in operations that need them to do such things as machining and working on assembly lines.
Greater Payload Capacity
Serial robots have a higher payload capacity. That's why they are commonly used in applications that require engagement with the automotive industry and heavy manufacturing.
Diverse Configuration Options
The arm configuration of a serial robot can be easily modified and adjusted to perform different tasks, meaning they are more beneficial in scenarios where different options are necessary.
Key Applications for Parallel Robots
Pick-and-Place Applications Delta robots can operate at much faster speeds, utilized in high-speed pick-and-place applications for electronics manufacturing and drug/pharmaceutical manufacturing.
Surgery Several parallel robots such as the Stewart platform are found in robotic surgery.
3D Printing Parallel robot applications in robotics for 3D printing provide greater printing accuracy.
Key Applications for Serial Robots
Manufacturing Assembly Lines Articulated robots apply to the majority of manufacturing assembly line applications to either weld, paint, or package; they have greater flexibility with greater payload capabilities.
Dangerous or Heavy Tasks Industrial robot arms are used for tasks that require much heavier lifting and rehabilitation efforts.
Automotive and Aerospace Manufacturing
Serial robots are often used for cutting, drilling, and fusing in the sectors of power and flexibility.
When to Use Parallel Robots vs Serial Robots?
- Parallel Robots are used in situations where speed, accuracy, and stiffness are required. Surgical robotics, 3D printing, and anything that requires high precision are examples.
- Serial Robots are used in flexible situations and when larger work envelopes are available, and there is a possibility for larger payloads. Manufacturing assembly, machining, and welding are examples.
Conclusion
Ultimately, the decision to use a parallel robot vs a serial robot depends upon project goals. Where space and limited payloads are not advantageous, a parallel robot is an ideal choice for quick, precise performance. If you want a thorough knowledge of robotics and industrial use, Warsonco Robotics will use its knowledgeable assessment to recommend and help you decide on suitable robotic systems.