Robotic Palletizer Installation & Training – A Detailed Guide
Robotic Palletizer Installation and Training: Getting Started with Automation
Why do Robotic Palletizers Works Well for the Businesses? At factories and warehouses, they automate work. But robots must be installed well. But people need to learn to use them, too. The most important thing is installation and training. A great installation ensures that the robot functions correctly. Training well enables people to utilize it safely and effectively. This article discusses Robotic Palletizer Installation & Training. This will elaborate on how to do this. It will explain why each is necessary.
Preparing for Robotic Palletizer Installation
How to Prepare for Robotic Palletizer Installation. You must prepare a robot before you install one. If you prepare correctly, installation can be easier. It also makes for a seamless introduction. Planning is the first step.
Preparing the Robot Installation Site in Your Factory
The installation site must be prepared. The floor must be level and strong. Clear the area of obstacles. Make sure that you have a sufficient power supply; There should be enough light in this work area. Site preparation is important for a safe and stable robot.
Ensuring Safety Measures are in Place Before Robot Installation
Make sure all safety measures are in place before installation. During installation safety measures play a vital role. Erect safety barriers around the installation zone. Tell people to use safety signages. On the ground, ensure that all individuals are aware of safety protocols. These safety tips should be followed during the installation process. Installers and workers are protected through safety measures.
Unpacking and Inspecting Your New Robotic Palletizer System
Your robot will have been housed carefully with filler packaging inside. Check for damage that may have occurred during shipping. Ensure all the parts are included. Report any damage or missing components immediately. You also confirm all is present and functional, via inspection.
Guidelines for Physical Installation of Robotic Palletizers
Secure Mounting of the Robot Arm and Base to the Floor
You need to mount the robot arm and base securely it. Follow the manufacturer's instructions. If you are dealing with tools and hardware, use the right tools. The robot base must be bolted to the floor. A stable base is needed for accurate robot operation.
Assembling and Attaching the End-of-Arm Tooling (EOAT) or Gripper
The EOAT or gripper is what the robot picks the products up with. Follow the instructions to install the gripper. This should be held securely by the robot gripper. Test the gripper so it will work properly. We have already seen how the right gripper is a must when it comes to picking and placing products.
Installation of Safety Fencing and Light Curtains for Workplace Safety
Safety fencing and light curtains prevent people from entering a dangerous area. Add safety protection around the robot work cell. Install light curtains to monitor entry into the workspace. Ability to connect Safety devices to the robot controller. Check that all safety systems are working correctly. The significance of safety systems in work areas.
Connecting the Power Supply and Air Supply to the Robot System
Robot Power and Air Robot powered up and sometimes air supply is required. Power up the robot by connecting the main electricity source. If you are using pneumatic grippers, connect airlines. Verify that connections are secure and correct. Robots require the appropriate supply of air and power to operate.
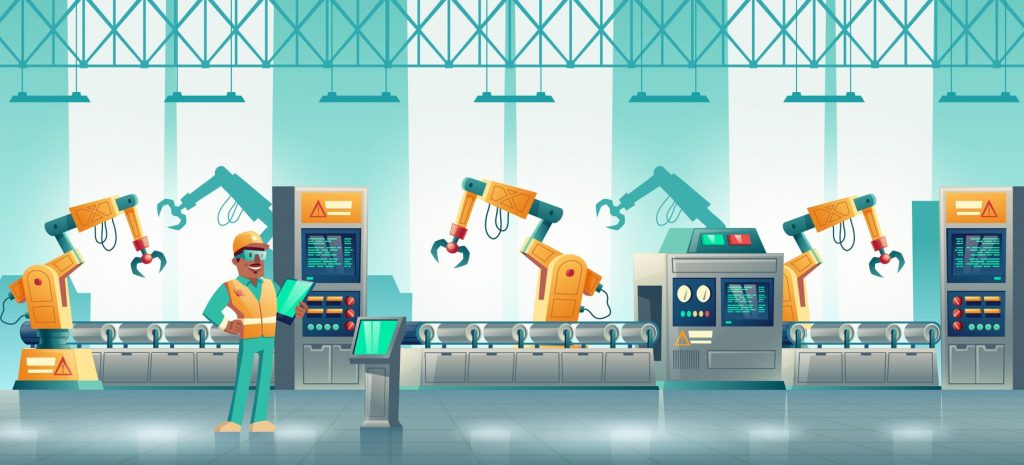
Deployment and Integration of the Robotic Palletizer System
Integrating the Robot Controller with Existing Conveyor Systems
Controller Integration with Conveyor Palletizers frequently works in conjunction with conveyors. Attach the robot controller to the conveyor system. This is to enable the robot to take products from conveyors. Integration allows the product to flow smoothly to the robot. Automated Material Handling Convenience Through Conveyor Integration
System Integration with Warehouse Management System (WMS) or ERP
WMS or ERP the robot must be connected. This facilitates communication data transfer between the robotic system and the central systems. Data includes pallet counts and error logs. WMS/ERP integration delivers actionable operational data. All in all, system integration overly enhances warehouse management.
Software and Communication Protocols Configuration for Optimal Performance
Configuration for Robots Handling Software Factory-configured, once set up, will just work – for any robot you want. Establish data-sharing communication protocols. Define pallet patterns and robot movements in the software The robot will not work until proper software is installed.
Testing System Integration and Overall Data Flow Verification
Data Flow Testing Test the whole structure after integration Make sure data correctly flows between the robot and other systems. Testing communication with conveyors and WMS/ERP System testing ensures all features collaborate fluently to give a great user experience. Well-tested end-to-end shows that there is integration.
Training Personnel for Effective Robotic Palletizer Operation
Operator Training for Basic Daily Robot Operation Tasks
Daily use is learned with operator training You are driven down and trained on which way to go. Train them to monitor robot performance. Teach them to deal with the basic alarms and errors. The operators are well-trained to work with these robots.
Routine Inspection and Preventative Maintenance Training for Staff
Training for Routine Checks and Upkeep Maintenance staff should be trained in robot upkeep. Teach them to perform preventative maintenance duties. Train them to lubricate, clean, and inspect the robot. Teach them how to spot faded components and swap them out. Robots tend to last longer if they are properly trained in maintenance.
Comprehensive Safety Training for Robotic Work Environments
This Safety Training is needed for Anyone Who Works Around Robots Safety training is essential for everyone who works with robots. Train staff on robot safety protocols. Educate them on safe zones and emergency stops. Educates and instructs about risks and how to prevent accidents. Comprehensive safety training ensures employees’ safety. Our robot environments require the utmost safety training.
Advanced Training for Robot Programming and Troubleshooting
Enhanced focus on coding and debugging. Some Staff Will Need this including programming robot motions and patterns. Advanced training also prepares you for troubleshooting complex issues. System optimization and complex repairs require advanced skills. Emphasis on in-house expertise development through advanced training.
Conclusion
Even if training and installation are in place for a Robotic Palletizer, they are both a major investment. Correct installation helps the robot function properly at the very beginning. Complete training enables your team to utilize and service the robot. Good installation and training also minimize downtime and maximize productivity. Warsonco Robotic Palletizer Installation & Training is an investment, so be sure to allocate funds for installation and training. These are important steps to gain longer-lasting advantages and good ROI on your automation journeys.