Parallel Robots vs SCARA: Explore Speed and Accuracy Robots
What are Parallel Robots and SCARA Robots?
Parallel robots are essentially defined as manipulators with multiple arms extending from a single base connected to a common base. They function on a parallel kinematic system in which such "arms" work simultaneously to adjust the location of the end-effector. A SCARA robot (Selective Compliance Assembly Robot Arm) is a serial robot with specific kinematic characteristics that create its name and allow it to move horizontally with rotary and linear motion. SCARA robots are commonly used for assembly and material handling applications where throughput and repeatability are critical. This article describes the difference between parallel robots vs SCARA.
Delta Robot - ZhiSheng Series: The Best Parallel Robots
The Delta Robot - ZhiSheng Series (WSC 600DJ/800DJ/1000DJ) is one of the top robots on the worldwide market, high-speed precision for today's modern manufacturing environment for the most effective and flexible state-of-the-art solution for any production line needing it.
Engineered for Effectiveness and Flexibility
Meets all expectations required in automation tasks from pick and place, assembly transfer, packaging, etc. ZhiSheng Series is a modular configuration, which means it can be tailored to specific needs and applications. The flexibility of the robot makes it easy to blend with any current assembly line, allowing for natural workflow and increased efficiency.
Easy Operation and Low Maintenance
Another critical feature of the Delta Robot is low maintenance and easy operation. This is a cost-effective option for companies looking for seamless operating automation solutions, as easy operation allows for immediate setup while low maintenance ensures that unnecessary disruptions are limited. This means companies can rely on productivity without excessive downtime for repairs.
The Best Robotic Solution for Your Business
If your company needs increased production capacities with high-quality assurance, the Delta Robot - ZhiSheng Series is the best robotic solution in the world to increase operational efficiency.
Kinematic Comparison: Parallel vs SCARA Robots
Control is essential for programming joints and ensuring optimal application performance. The more information a robotic programmer has to map out and sketch the joints and movement challenges, the easier it is to create the robot.
- Parallel robots are relatively easy to control with kinematic analysis because of their reduced DOF, meaning that there's less to design and consider for potential challenges. Images and drawings can be mapped out and CAD developed with fewer iterations needed.
- SCARA robots may have more complexities due to the additional DOF that requires consideration in terms of joint safety and motor placement for collision avoidance. CAD may take a few iterations to finalize as the complex needs of all 4 directions must be fully assessed.
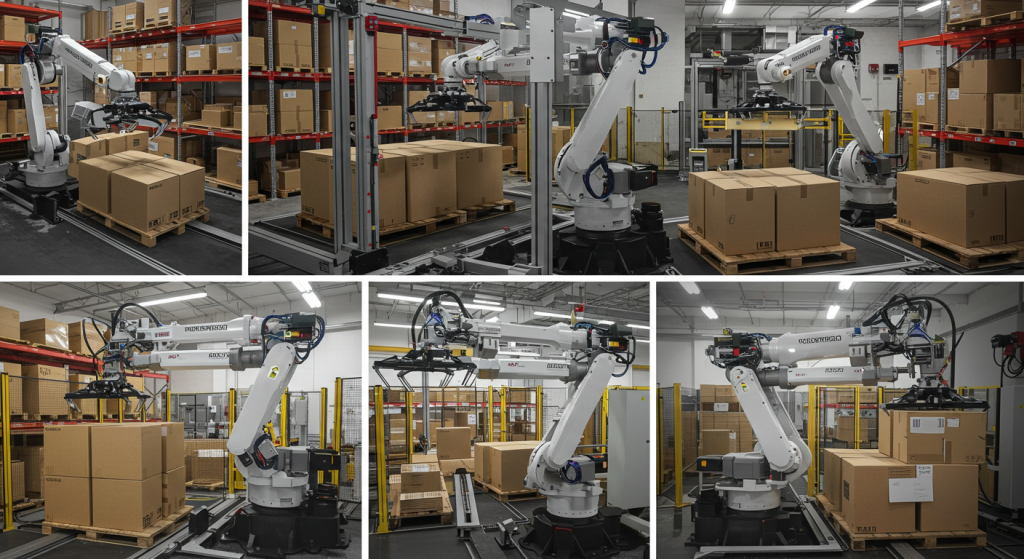
Degrees of Freedom (DOF): Parallel Robots vs SCARA Robots
- Parallel robot: The degrees of freedom associated with each one differ when it comes to robot efforts. For example, the Delta parallel robot has three DOF, which means it operates in three-dimensional space but, thanks to specific degree applications and configurations, is more adept at maneuvering within its defined work envelope.
- SCARA robots: Nevertheless, SCARA robots usually have four degrees of freedom, where the ability to maneuver both along and perpendicular to a defined pathway is advantageous for parts that require horizontal or vertical transfer from one area to another; SCARA works well for assembly line automation and simple material handling.
Robot Workspace Comparison
The work envelope, or workspace, describes the range with which a robot can access and maneuver.
Parallel robots: Thus, the work envelope associated with each type differs. For example, parallel robots tend to have a more finite work envelope. The reason for this is that specific applications like the Delta are designed to create a sturdier frame via a more compact configuration to allow such accuracy to be afforded to workspaces that are smaller and require more on-target efforts like electronics or medical part assembly.
SCARA robots, on the other hand, tend to have a larger work envelope, which allows for greater flexibility in a variety of industrial applications. They are suitable for tasks like packaging automation, where the robot needs to move across a larger area efficiently.
Payload Capacity: Parallel Robots vs SCARA
- Parallel robots are designed for smaller footprints and more precise movements, so they tend to make up for a reduced payload capacity. In confined environments or when working with small parts, a lighter payload is permissible. Within a smaller working volume, these parallel robots can support up to 12 kg.
- SCARA robots have a more robust construction and consistent success across larger work envelopes. Therefore, they are capable of operating at higher tolerances and still staying on par for similar precision. SCARA robots are versatile and strong, offering an increased payload capacity of 50 kg across an expanded operating range. They're typically the better choice in a manufacturing environment where payloads are required to be more substantial.
Speed and Acceleration: SCARA vs Parallel Robots
Another comparison factor of performance is speed and acceleration.
- Acceleration is a major factor in operation and parallel robots have higher speeds when needed for certain applications such as high-speed packaging or sorting.
- SCARA robots may not be the fastest in certain applications compared to parallel robots, but when it comes to assembly lines and more, they still increase speed exponentially. SCARA robots excel at high-speed assembly that requires repetitive tasks with little need for complicated routing access.
Cost Analysis: Which is More Cost Effective?
Cost-effective comparison means needing to find a balance of upfront robot pricing as well as maintenance and operational pricing down the line.
- Parallel robots tend to have a more expensive upfront investment due to the engineering process and higher precision capabilities. However, they tend to be reliable with low maintenance needs for high precision use, which makes them much more cost-effective down the line if their application requires such accuracy.
- SCARA robots are cost-effective when compared to parallel robots as they have a lower initial investment cost, especially when compared to general assembly. They are easily maintainable for repairs and because they can handle heavier payloads, SCARA robots are useful for automotive and electronics production.
Ease of Programming/Control: SCARA vs Parallel Robots
- Parallel robots: Joint configuration runs through robot control systems for more complicated robotics control systems needed for parallel robots due to their highly complex kinematics. Everything is run through robot simulations and highly specialized control software to make necessary functions happen.
- SCARA robots: Robots can be programmed with relative ease due to less complex joint configuration. Less specialized robotics control systems are needed, programmed more for expected motion and easier use where end effector design is focused on more.
Conclusion
As for the comparison and contrast between parallel robots vs SCARA robots, it all depends on your application needs. Parallel robots are ideal if you need precision, speed, and accuracy and don't need to worry about payload. For more information on industrial robotic solutions, visit our website at Warsonco Robotics. Our experts have years of experience in helping industries select the best robotic solutions.