Parallel Robots vs Cartesian Robots? Key Differences Insights
What are Parallel Robots?
Parallel Robots (also known as parallel manipulators) are robotic systems comprised of multiple arms that work simultaneously and independently before converging at a joint point on a common base. They have a fixed platform while the arms move and help generate the end effector motion. The most well-known type of parallel robot is the delta robot, which operates quickly during pick-and-place activities. This article explains the difference between parallel robots vs cartesian robots.
Features of Parallel Robots:
Kinematic Structure: The configuration of the actuators in parallel allows for increased relative control of positioning.
Degrees of Freedom: Parallel robots have degrees of freedom ranging from 3 to 6.
Stability and Rigidity: Many parallel robots are symmetric, which provides for dynamic stability.
Payload Capacity: They can have high payload capacities relative to their size since they work in conjunction with multiple arms.
What are Cartesian Robots?
Cartesian robots also known as linear robots employ a rectangular coordinate system. Their motion consists of linear three-axis movements: X, Y, and Z. The robotic arm moves along the predetermined axes. It's often utilized for tasks that require simplicity and repetition, including packaging, assembly, and material handling.
Features of Cartesian Robots:
Kinematic Structure: Employ linear actuators for operation by moving on a straight line; simple motion and predictable movement are their hallmarks.
Degrees of Freedom: 3 degrees of freedom with the possibility of additional axis configurations.
Payload Capacity: They are stable in precision-based applications; higher payload capabilities than parallel robots are rare.
Simple Design: Easy to construct and debug due to linear orientation.
Parallel Robots vs Cartesian Robots: A Comparison
Now that we understand what parallel and Cartesian robots are, let's compare them in the following categories:
Kinematics and Dynamics
- Parallel Robots: Kinematics is somewhat complex. They use the added rigidity and stability, especially when dynamic loads are involved. They process speed-related tasks faster.
- Cartesian Robots: Kinematics is more straightforward. They generate predictable, smoother motion. However, the parallel kinematics approach may not be as fast or flexible.
Accuracy and Precision
- Parallel Robots: Parallel robots are more accurate than Cartesian robots when execution is high precision/high speed. The ability to avoid errors with dynamic use is lessened because of the design.
- Cartesian Robots: High precision is possible with perpendicular movement along the three axes; however, slight inaccuracies can be generated if tasks are highly dynamic due to mechanical play in the joints.
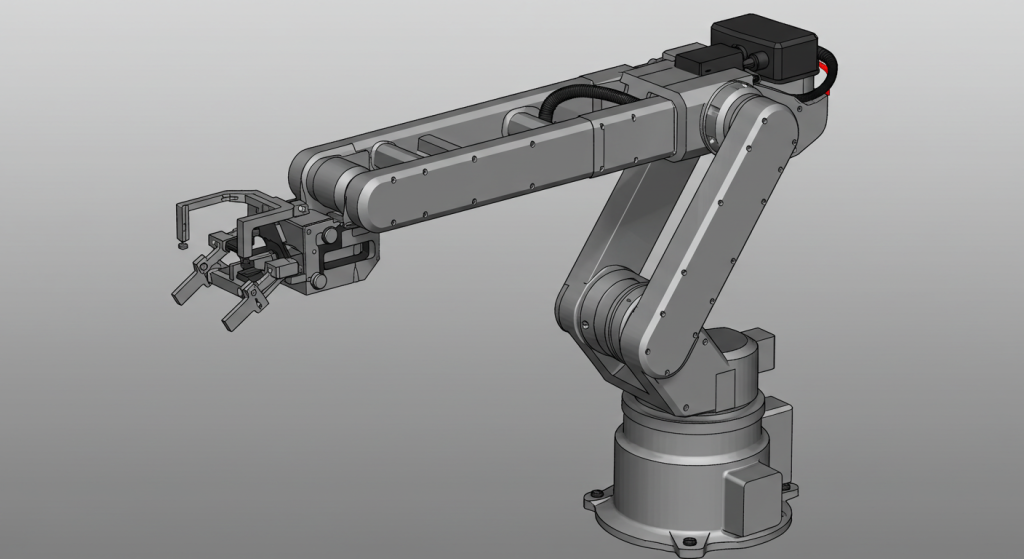
Speed and Throughput
- Parallel Robots: Parallel robots (delta robots, etc.) are incredibly fast and excel in high-speed pick-and-place and packaging applications.
- Cartesian Robots: Cartesian robots can be fast in select applications but on the whole are slower than parallel, especially when speed and maneuverability are needed.
Workspace
- Parallel Robots: Parallel robots usually have a smaller workspace than Cartesian but can accomplish intricate tasks in that smaller space with high accuracy.
- Cartesian Robots: Cartesian robots have a large work envelope and perform very well in applications needing extensive movements in a correspondingly sized larger area.
Design and Complexity
- Parallel Robots: The design of parallel robots is more complicated with multiple arms and actuators; however, their performance is better with accuracy and stability for certain applications.
- Cost: Cartesian robots are expensive to create, simple to maintain, and relatively easy to operate based on a more simplistic design. These elements decrease overall costs and why companies that cannot afford too much in automation generally seek Cartesian systems.
Cost
- Parallel Robots: Parallel robots are expensive when comparing costs. They have a more complicated design and the materials used to manufacture them are pricier. But they are a worthy investment for precise applications.
- Cartesian Robots: Cartesian robots are often more affordable, especially for simple automation tasks. Their simple design and fewer moving parts contribute to a lower price point.
Pros of Parallel vs Cartesian Robots
Pros of Parallel Robots
Faster operation: Parallel robots can do things faster which makes them ideal for needs requiring operation in a quick amount of time.
Increased Accuracy: A more rigid design allows for parallel configurations to be more accurate, especially on high-output tasks.
Increased Payload Capability: Parallel configurations can work with more massive loads and still achieve some level of speed and accuracy.
Pros of Cartesian Robots
Easy to use: Cartesian configurations are easy to configure and easy to maintain making them cost-effective for low-level tasks.
Bigger Work Envelope: The Cartesian configuration allows for a bigger work envelope based on linear motion abilities.
Price: Cartesian robots are generally less expensive because there are fewer components and they are less complex.
Applications: Parallel vs. Cartesian Robots
Both types of robots are utilized across industries for various applications with successful results:
Parallel Robots:
• High-Speed Pick-and-Place: A type of parallel robot called the delta robot is commonly used for high-speed pick-and-place in food packaging and electronics manufacturing.
• 3D Printing: In the additive manufacturing world, parallel robots are used to efficiently create models for rapid prototyping.
• Surgical Robotics: In medically sensitive arenas where precision is essential, parallel robotics are used for minimally invasive surgical procedures.
Cartesian Robots:
• Assembly Lines: These robots are used in assembly lines for replication-type motions such as moving items from one station to another.
• Material Handling: Warehouses and distribution centers use Cartesian robots for picking, sorting, and palletizing.
• CNC Machines: Any systems that require precise linear movement rely on Cartesian robots, including CNC machines.
Conclusion
Ultimately, choosing the parallel robots vs Cartesian robots depends on these considerations. For more information on robotic machinery and solutions for your application, visit Warsonco Robot Solutions. An analysis of our design, functionality, and application suitability will reveal which robotic system is appropriate for organizational needs. Our complete catalog and company summary of Warsonco Robotics. Discover how Warsonco Robotics can revolutionize your business with cutting-edge robotic solutions. Warsonco Robot Parallel is used in food, chemical, pharma, beverage, dairy, quick-frozen, 3C, daily chemicals, logistics, and a variety of other industries for automated packing solutions. Reach out now.