Parallel Robots Solution: Boost Efficiency & Precision
What is an Automation Parallel Robot Solution?
Essentially, an automation parallel robots solution is a robotic solution that comes from parallel kinematics that provides high accuracy and high speed of movement. Parallel robots feature multiple actuators working simultaneously in parallel as opposed to a series of linkages providing control. In many cases, they offer superior accuracy and speed over traditional serial robots. One of the most well-known configurations of parallel robots is called a Delta robot. Delta configurations are extremely common in pick-and-place, packaging, and assembly automation applications because they're extremely fast and extremely accurate.
Key Technologies Behind Automation Parallel Robots
Parallel Kinematics:
The foundational technology that supports automation—parallel robots employ parallel kinematics. Where standard serial robots use one arm, and one linkage to perform required tasks, kinematic systems use multiple—and sometimes countless—individual actuators to move the end effector, which is the ultimate tool for application. This allows for more control and more freedom over complex paths of motion, meaning increased levels of throughput and reduced cycle time.
Motion Control and Servo Systems:
The technology needed for advanced motion control goes hand-in-hand with servo systems for the expected levels of precision that make parallel robots such a desirable option for implementation. Motion control systems depend on sensors and feedback loops to succeed. The servo systems linked to the motion control systems ensure that expected positioning occurs instantaneously and without lost motion. As a result, parallel robots have exceptional repeatability—which is perfect for precision engineering applications and high-speed projects.
End Effectors and Robotic Vision:
Many benefits of automation parallel robots come from having end effectors and robotic vision. Without end effectors—which are tools at the end of the arm of a robot—many automation solutions would be less effective and omnipresent. End effectors can include anything from grippers and suction cups to the tools needed to put parts together. Furthermore, many advanced parallel robots have robotic vision, enabling them to "see" what they're doing, which comes in handy for solutions in packaging automation and material handling.
Force Sensing and Trajectory Planning:
Compounded by force sensing—where the robot can understand how much pressure it's putting forth during the interaction—and the trajectory planning software of the automated solution—that predetermined use of movement ensures every action is planned for the greatest benefit. Efficiency and precision are required in pick-and-place automation and assembly automation.
Advantages of Automation Parallel Robots Solution
The benefits of using parallel robots for industrial automation are clear. They offer the versatility, speed, and accuracy required for contemporary industrial production processes.
Accuracy and Speed:
Where accuracy and ultra-high speed are required for highly repetitive tasks, parallel robots provide both. Parallel robots are designed for strenuous, repetitive tasks like automated pick-and-place, packaging, etc. When combined with an increased growth rate, parallel robots with high accuracy and quick cycle times can bring positives to automotive manufacturing and aerospace automation.
Increased Growth and Productivity:
Parallel robots increase growth and productivity when they can accomplish tasks quicker than traditional robots. With effective multi-axis control, they accomplish more with fewer movements, allowing parallel robots to move more quickly with reduced cycle times. Increased growth occurs when productivity is increased, and any industry aiming for increased scalability appreciates this.
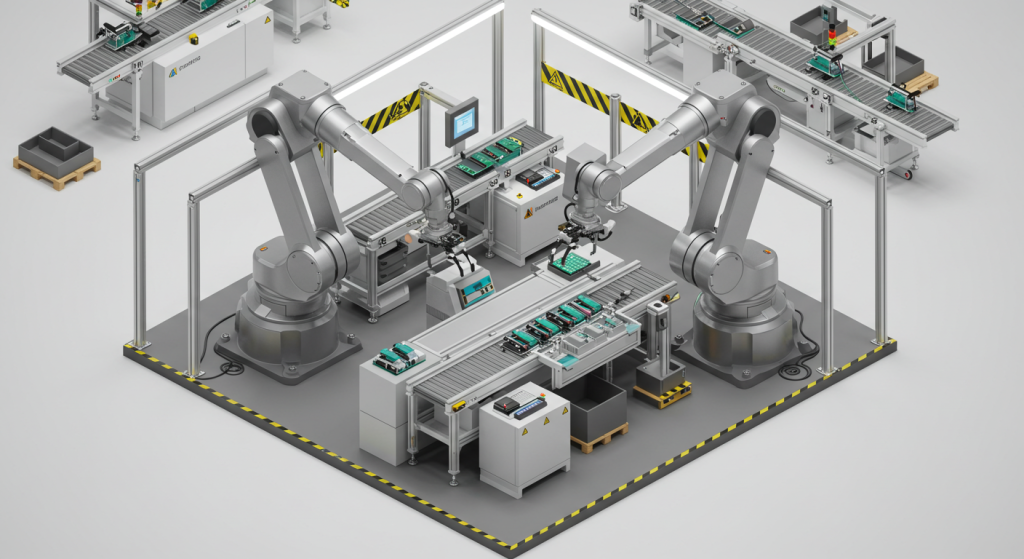
Reduced Cycle Time and Cost:
One of the anticipated features of automation in the future is reduced cycle time. Parallel robots are constructed to deliver such results as quicker turnaround times enabling organizations to save time—and in turn—money. For example, a parallel robot can be implemented via robotic system integration solutions or turnkey automation options to create a more cost-effective environment.
Multi-Purpose Automation:
One of the hallmarks of parallel robots is their ability to be used for many purposes. Whether for medical robotics, surgical robotics, or industrial automation, parallel robots can be customized and configured to fit many needs. Organizations that seek this attribute will be more likely to have a competitive edge in their environments.
Requires Less Footprint:
Generally speaking, while some parallel robots may be larger, many of these automated systems are constructed to work in smaller footprints. This is critical for robotic work cells and automated assembly lines where operations have little space to work.
Applications for Automation Parallel Robots
The implementation of the automation parallel robots solution can be applied to various industries where precision, speed, and flexibility needs arise. Below are some of the pertinent industries that would use this innovative technology:
• Industrial Automation: The need for customized industrial solutions where parallel robots improve industrial automation for automotive robotics boast the high speed and accuracy features necessary for assembly line processes and material handling.
• Manufacturing and Assembly Automation: From customized robotic solutions for packaging to automated pick-and-place solutions, parallel robots are used on almost all assembly lines to create better product uniformity with reduced need for human interaction.
• Medical Robotics: The parallel robot provides the medical robotics solution for surgical robotics systems which boast increased precision and the proper flexibility to execute delicate procedures.
• Aerospace and Automotive: High-speed parallel robots are increasingly used in aerospace for automated assembly and inspection of small components requiring extreme precision and in the automotive industry for similar assembly applications and high-volume production of small components.
How to Integrate Parallel Robotic Systems?
The easiest way to integrate a parallel robotic system into your assembly or production line is to work with a trusted professional provider of automation solutions Warsonco. Whether you're in the market for robotic integration or complete turnkey automation solutions, professional engineers will design, develop, program, and deploy a solution tailored to your requirements. A reputable provider will grant you access to the right customized robotic solutions while guaranteeing your robots are fully optimized for the intended purpose.
In addition, using kinematic simulation software allows you to generate a digital twin of what a parallel robot would do in your environment to ensure all necessary operational requirements are met before going live. In addition, robotic maintenance and automation consulting solutions ensure your robotics continue to function as required over time.
Conclusion
The automation parallel robots solution is changing the world. The fact of the matter is, with the opportunity to accomplish high-accuracy tasks in such a short period, these robots are not a luxury anymore but a necessity for any company that wishes to remain competitive in the global arena. Parallel robots offer the speed and accuracy that a fast-paced world and marketplace requires whether it's flexible automation or the need for rapid processing.
To discover how to integrate parallel robots into your process, visit Warsonco Robots.