Parallel Robots for Pick and Place: Explore Robot Solutions
What are Parallel Robots for Pick and Place?
Parallel robots are recognized as parallel kinematic machines (PKM). They operate differently than a traditional robotic arm based on a serial (a line of joints sequentially) approach. A parallel robot utilizes several actuators attached to a fixed base, as well as a closed-loop kinematic chain (the existing joint). The advantage of this design is a more stable, quicker, and more accurate experience. Parallel robots for pick and place essentially means that things are picked from one site and placed in another, whether on factory assembly lines, in product packaging, or sorting small parts and components. They have incredible throughput and precision.
How to Choose the Best Delta Parallel Robot for Pick and Place Applications?
Speed and Throughput: How Fast Does the Robot Need to Be?
For pick-and-place scenarios, speed is often directly correlated with the potential for productivity. The faster a robot can accomplish its task, the faster it can accomplish more work within a small timeframe. The WSC 1000D operates at 60 to 120 cycles per minute depending on the application, an incredibly high range for not only throughput but also accuracy. Think about your workplace—food packaging, automotive assembly, electronics production—and the WSC 1000D can drastically reduce the cycle times needed for such touchy projects, increasing throughput and exceeding expectations without compromising quality.
Product Longevity: How Long is the Production Welcome for Robotics?
Key takeaway: robots today can last a lifetime, but your robotics systems may need updates after several years down the line. Automated robots are known to last longer than collaborative ones since they don't have to collaborate with humans, but a lot depends on the stress placed on the robot, too. Smoother operations yield better longevity. Pay attention to these factors when selecting your robot.
Repeatability: Are Precision and Accuracy Key?
In many pick-and-place applications, repeatability is critical. The WSC 1000D has a repeat positioning accuracy of ±0.05mm, so every piece gets placed just right. For instance, this is the perfect robot for electronic assembly or pharmaceutical packaging where the tiniest deviance can result in major errors in production. Bottom line: If you need accuracy on your side, look for a robot with repeatability. The WSC 1000D Delta Parallel Robot makes the same process work successfully over and over again after repeated cycles, making it perfect for even the most demanding of jobs.
Travel Range: Does the Robot Need to Cover a Lot of Ground?
Another key consideration when it comes to a parallel robot is the travel range. The further a robot travels, the more flexible it will be in covering tasks that require extensive distance. The WSC 1000D has a travel range that is impressive, meaning it can exceed larger distances along the assembly line, making it easier to adjust to various materials in one operation.
Durability and Reliability: Will the Robot Last?
Reliability is critical when choosing a durable solution for high-speed pick and place. There are quality materials and robust parts that make up the WSC 1000D Delta Parallel Robot, which means it can perform at an industrial level without a hitch. Day and night, in harsh temperatures, the Delta Parallel Robot is so durable it makes it an option for consistent operation over time.
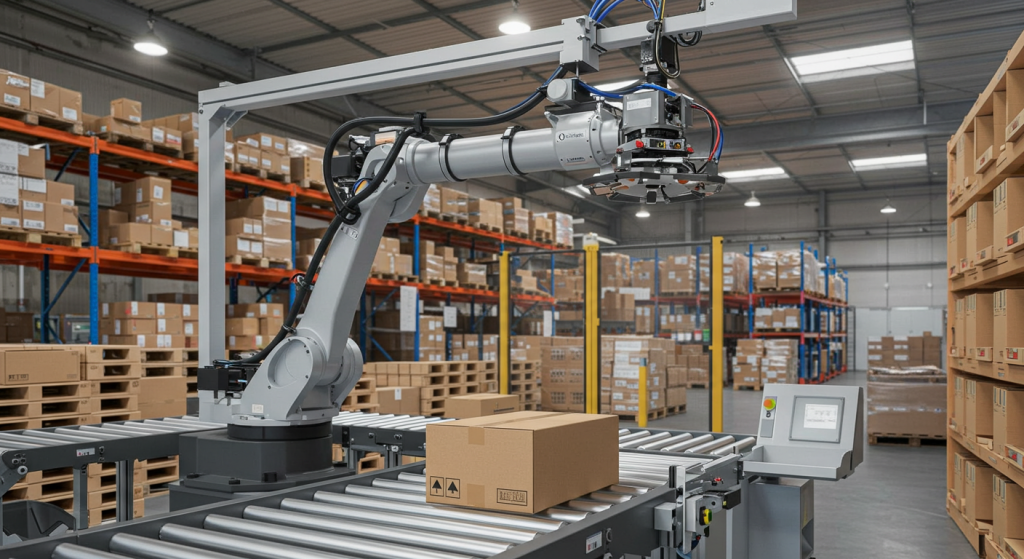
Why the WSC 1000D Delta Parallel Robot is Ideal for Pick and Place Applications?
Choosing the ideal parallel robots for pick and place operations is crucial for improving efficiency, accuracy, and production quality. The WSC 1000D Delta Parallel Robot is the leader in many categories: speed, accuracy, payload, and ease of integration make this a flexible option for industries ranging from food packaging to electronics, even pharmaceutical assembly. Ultimately, assessing important factors such as speed and payload, accuracy, and range of motion, allows companies to determine the best fit for their production needs. The WSC 1000D offers capabilities that place it above the rest and make it the perfect choice for high-speed pick and place. Contact Warsonco Robotics today to ask about the WSC 1000D Delta Parallel Robot and discover how this cutting-edge solution can transform your automation!
Technical Details: How Do Parallel Robots Work?
To appreciate what parallel robots can do, it's important to know how they work. Parallel robots work based on their kinematic structure and an array of temporally displaced actuators. The highlights include:
• Inverse and Forward Kinematics:
In control theory, inverse kinematics is the computation of where each actuator needs to be positioned (angles, speeds) to achieve the desired position of an end-effector. Forward kinematics is the analysis of the achieved positioning of the end-effector based on decided actuator positioning.
• Degrees of Freedom (DOF):
Parallel robots are made up of six degrees of freedom which allow them to move in various directions and orientations, allowing for extremely high levels of precision.
• Robot Control and Motion Control:
Advanced programming for the robotics and motion control schemes that enable the robot to do what's required and include servo motors, linear actuators, and rotary actuators.
Conclusion
Parallel robots for pick and place are revolutionizing multiple industries with their fast, precise, and adaptable solutions. We are the preferred solution for any assembly line needing high efficiency due to the large payload capabilities and precise tolerances of 1/1000th of an inch, as well as the capability to use them with other automated solutions. Whether you're in the food packaging industry, electronics, or pharmaceuticals, a parallel kinematic machine can provide you with the efficiency and reliability that you seek. Consider Warsonco Robotics as a starting point for any organization to implement these solutions, as we provide customized automated solutions that integrate into your existing assembly line and bring pick and place precision to your organization.