Parallel Robots for Packaging: Boost Speed & Efficiency Today
What are Parallel Robots?
Parallel robots—kinematic machines or multi-axis manipulators—are a specific type of robotics that can execute multi-axis functionality with precision. The machines are defined by closed-loop kinematic chains, meaning they can operate in multiple directions at the same time. Thus, parallel robots for packaging are used in scenarios where rapid, consistent, and precise motion and function are needed. Within packaging, parallel robots help the packaging process by automating some of the functions related to handling, assembly, sorting, and packaging. Used in packaging, sorting, pick-and-place applications, and more, this robot can do everything and do it fast. This is a very efficient, effective machine for various industrial applications.
Delta Parallel Robot WSC 1000D: High-Speed Precision for Automated Packaging
The Delta Parallel Robot WSC 1000D is a high-quality operative machine for those needing fast testing and execution without error. It offers 60 to 120 cycles per minute. The WSC 1000D is a professional packaging and manufacturing robot that exerts a 12kg load capacity effortlessly. The travel distance is extensive yet application-specific depending on the requirements of the aligned project, which is universal across all industries, as food, pharmaceuticals, and electronics can all use this device effectively.
Overview of the Delta Parallel Robot WSC 1000D
This machine features a complex parallel kinematics system that allows it to operate at high speed when picking, packing, and assembling. In addition, this robot is constructed from heavy-duty materials which allow for quality output consistency in the most demanding environments.
Features of the Delta Parallel Robot WSC 1000D
High-Speed Capabilities
One of the greatest features of the Delta Parallel Robot WSC 1000D is its high-speed capabilities. This machine can perform anywhere between 60 and 120 cycles per minute. Such high-speed results are ideal for assembly lines that need a fast momentum to stay efficiently productive. Reduced cycle times mean increased productivity levels allowing manufacturers and industries to keep up with increased demand forecasts while never sacrificing quality.
Impressive Payload Capabilities
The payload capabilities of this machine range from 3 kg to 12 kg. Therefore, it's able to work with a number of different lightweight and heavyweight products, from small electronic components to heavier weights experienced in the food processing sector. This means that this parallel robot will offer consistent and effective operation with no problem across various products and initiatives.
Large Travel Range
The Delta Parallel Robot WSC 1000D has a large travel range which makes this robot more versatile. The fact that it can travel larger distances means that it's able to reach further in its operations, focusing on larger areas and larger workspaces without the need for multiple robots. It can seamlessly fit into an already existing assembly line or production line and get the job done effectively without overexerting. Whether it has to travel far for detailed assembly or far for pick and place and packaging, the large travel range facilitates the function.
Precision and Accuracy
The Delta Parallel Robot WSC 1000D is all about precision and accuracy. With precise control systems equipped, this unit only operates when it needs to operate and how much it needs to operate with a repeat positioning accuracy of ±0.05mm. This precision is important for small incremental adjustments, small parts integration, compound assembly, or sorting as less error is critical for sensitive operations in electronics, food services, or pharmaceuticals where safety and efficacy are always at the forefront.
Reliable Materials
The Delta Parallel Robot WSC 1000D is made of high-quality, durable materials and is assembled with reliable parts to ensure low failure rates. High-quality materials mean the robot can handle continuous use and intermittent assembly line activity, limiting downtime due to malfunction and maximizing productivity and throughput.
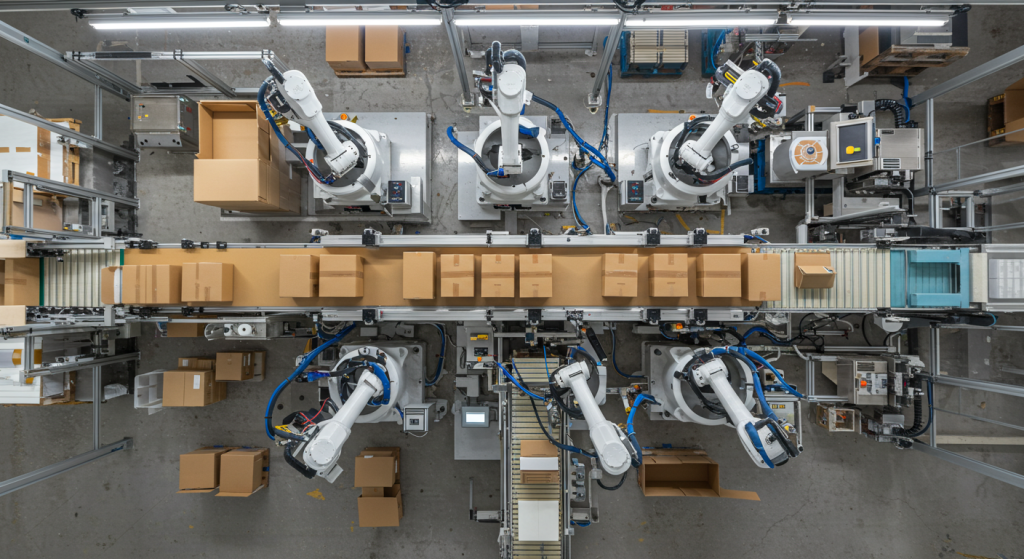
Uses for the Delta Parallel Robot WSC 1000D
Potential Industrial Applications of the Delta Parallel Robot WSC 1000D:
Packaging and Sorting
Industrial applications in which this robot could be beneficial include packaging and sorting. Any location where packaging and sorting need to happen at a high-speed capacity would be able to utilize this robot for better production. It could sort products by size—placing large products on one side and small ones on another—or it could sort by color and pack products into designated boxes.
Pick-and-Place
The Delta Parallel Robot WSC 1000D can be used in a setting where it needs to place small electronic parts into molds or food into smaller containers or onto conveyor belts. The sensitivity this robot possesses is operated for small electronic components as well as temperature-sensitive food-grade applications. Everything can be placed where it needs to be without damage, under the supervision of this robot.
Assembly Line Operations
Assembly operations in the automotive, electronics, and consumer goods industries also benefitted from such a robot. By increasing assembly line accuracy and efficiency, this robot reduces assembly time and costs, decreases labor costs by keeping in-house assembly costs lower, and increases overall productivity.
Pharmaceutical and Food Uses
In pharmaceutical as well as food and beverage industries, such a robot can lend a virtual hand in safe, proper actions taken on fragile and sensitive materials. Its increased precision and repeatability ensure consistent product quality, compliance with regulatory requirements in all fields, and proper quality for packaging.
Benefits of Parallel Robots for Packaging
While many types of robots can help package, parallel robots are preferred for several reasons:
Speed and Productivity
One of the most common reasons for utilizing parallel robots on packaging assembly lines is speed. They can do in mere seconds what a human takes a long time to do, which not only increases productivity but also minimizes turnaround time. This is vital in high-volume applications such as food and beverage packaging.
Extreme Accuracy
Packaging with the use of parallel robots requires precise operation. When a small error can cause a vast error in product numbers, using parallel robots to orient and set down products—or package them in a certain direction—will have an automated solution that provides the information that even the most precise human worker cannot keep up with over time.
Cost-Effectiveness
Packaging can require a lot of repetitive manual operations. This reduces the benefits of manual labor on the packaging line. Although robotics technology can be a significant initial investment, over time, reductions in manual labor needed create cost savings down the line.
Reliability
Parallel robots are built for reliability and when maintained, they provide zero-downtime operation. Their solid construction means they can operate continuously without the need for stopping production and delays that decrease effectiveness over time, which is crucial for high-speed packaging lines. Advanced Control Systems Real-time control of the robotic packaging and AI-enabled optimization allow parallel robots to make adjustments based on real-time data, improving their application and reacting to stimuli occurring within the manufacturing environment.
Conclusion
Parallel robots are revolutionizing the packaging industry's operation with speed, precision, and flexibility that traditional solutions cannot match. As technology develops and the need for faster, cheaper, more effective solutions grows, parallel robots will be at the forefront of the packaging industry's future.
To learn more about how a parallel robot can boost efficiency on your packaging line, visit Warsonco Robotics, your resource for robotic automation.