Parallel Robots for Material Handling: Applications & Benefits
Why is the WSC 1200D Delta Robot Such a Great Addition for Material Handling?
The WSC 1200D Delta Robot is changing what it means for businesses to handle material and automate efforts. The WSC 1200D enhances current opportunities by making sorting, packing, and placing products much better with increased precision, speed, and consistency. The parallel robots for material handling up to 120 times per minute, according to reports. Therefore, in places where rapid placement of properly placed items is necessary, the WSC 1200D can be found. It's commonly found in the pharmaceutical industry, among food producers, as well as in consumer electronics and daily chemicals as it allows companies to reduce human error and increase service potential for customers.
What Key Features of Parallel Robots for Material Handling are Unique?
Speed and Efficiency
Boasting 60-120 picks and placements per minute, this robot suits high-speed placements requiring rapid response. High-efficiency performance allows assembly lines to operate at their intended capacity without hindering production.
Material Compatibility:
The WSC 1200D boasts a payload of 3kg, 8kg, and 12kg, which means it works with various materials. It can apply itself to electronics and kinesiology as well as drug and food packaging.
Precision & Accuracy:
With repeat positioning accuracy at ±0.05mm, each task is completed with attention to detail. Whether packaging a tiny electronic device or sorting sensitive pharmaceuticals, the WSC 1200D offers an accurate approach to avoid defects in the end product or injury in the process.
Affordable Automation:
The WSC 1200D is an inexpensive way to add automated use to material handling activities. With increased productivity and reduced human error, industries save on labor costs and improve consistency of use.
Adjustable for Various Industries:
The WSC 1200D can be used across a myriad of industries from pharmaceuticals to food to everyday chemicals to electronics and hardware cutting. It can accommodate products of all sizes and shapes, from small pieces to larger needs, making it a great addition to any project assembly line.
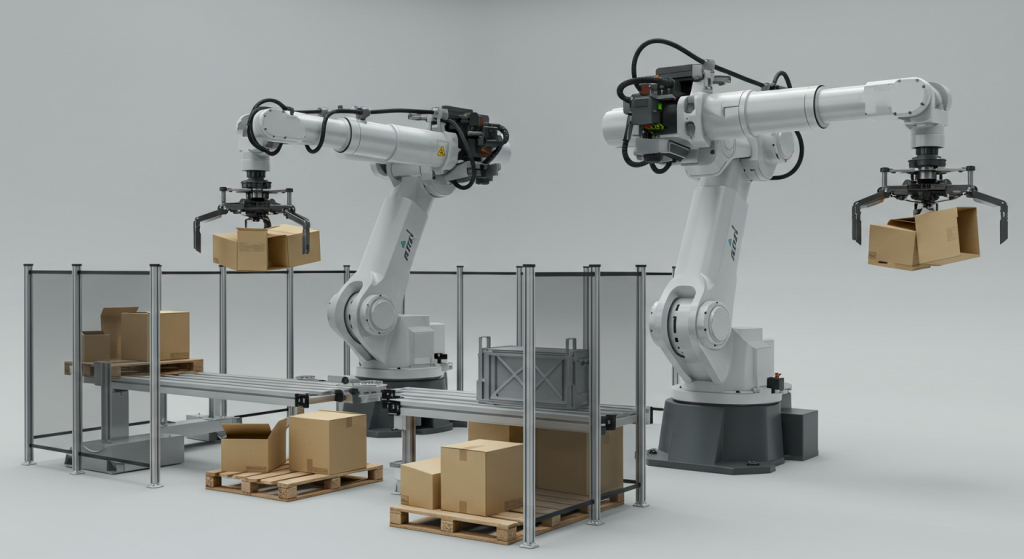
How to Choose the Right Delta Robot for Your Application?
There are various considerations when determining a Delta Robot like the WSC 1200D for your material handling requirements, and ensuring that you determine the best fit for your application isn't overwhelming so long as you consider the following.
Payload Requirements
One of the initial considerations in determining which robot is best for you is the payload of what your intention is to move. The WSC 1200D has a payload range (3kg, 8kg, 12kg) that services a variety of material needs. Just make sure to choose the one that accommodates the heaviest of your loading/unloading process to avoid excess and ensure the safety of operation.
Speed Requirements
The WSC 1200D operates at 60-120 times per minute. This is adjustable based on your needs during production. Should your warehouse require rapid movement of materials, this robot will enhance productivity and minimize stagnant times during production. However, should speed not be a requirement, a less expensive, slower operating unit may be more beneficial for your requirements.
Accuracy
For sensitive placements or projects in pharmaceuticals or electronics, you'll want a robot that positions with extreme accuracy. WSC 1200D has ±0.05mm repeat positioning accuracy, meaning sensitive or high-value parts will always be positioned accurately. If your industrial operation requires sensitive parts positioned with extreme accuracy, this is the robot for you.
Easy Integration into Existing Workflows:
WSC 1200D can join a working ecosystem without troublesome integration. It features inverted installation capabilities. If your assembly line is super-compacted or the robot will be installed in a non-flat position, this flexibility is critical.
Maintenance:
The parallel robots for material handling require minimal maintenance as it is a lightweight device that utilizes a spring mechanism for the durability and longevity of the robot itself. Look for a device that requires minimal accessibility to parts so maintenance will be kept in a less frequent manner while ensuring a durable, long-lasting robot.
Cost vs Benefit:
While the purchase price is essentially an investment/initial cost, the WSC 1200D Delta saves time and money in production, saves time on labor, and improves the quality of output, so the cost-benefit down the line is even more cost-effective. In addition, costs are taken into consideration with the WSC 1200D so that every size company, small or large, can reap the benefits of high-quality automated performance without an overly costly device.
Sectors Where the WSC 1200D Delta Robot is Applicable
Because the WSC 1200D possesses a variety of features, it is applicable in a variety of sectors:
• Pharmaceutical: The precision of a delta allows compliant handling and packaging of products while also satisfying compliance regulations of the pharmaceutical industry.
• Food Industry: Where machine operator speed and accuracy are coupled with reduced chances for contamination.
• Assembly: The physical configuration allows for proper alignment in packaging and assembling components with real-time quality assurance.
• Daily Chemicals: The physical configuration allows for packaging and assorting daily chemical products with required safety and rate of production capabilities.
Benefits of Material Handling with a Parallel Robot
There are numerous benefits to material handling when using a parallel robot, especially in an environment conducive to expansion and velocity:
Increased Production Rates
Material handling with parallel manipulators can yield increased production rates, attributable to the velocity of machine operation and no downtime; redundancy in throughput increases vast amounts.
Reduced Cycle Times
Increased Accuracy. Parallel robots operate on kinematics, which means they move with relative precision. From electronics assembly to pharmaceutical packaging, parallel robots perform the most precise efforts so that small parts are moved and manipulated exactly as needed.
Low-Cost Automation:
While the initial investment in a parallel robot is high, the low-cost automation that comes after far surpasses the investment upfront. With lower costs of labor and more dependable operations, a parallel robot saves money down the line.
Improved Versatility:
Parallel robots can be utilized for many different processes across many different industries, allowing businesses to use them for differing tasks as they grow or diversify automation opportunities.
Conclusion
Parallel robots for material handling are the future of automated warehousing and manufacturing systems. From faster production rates with less cycle time to enhanced precision, material handling robots can be found in any manufacturing setting—warehouse automation, packaging, automotive—and beyond. Contact industrial automation distributors and robotics integrators for on-site parallel robot solutions. WarsoncoRobotics keeps you abreast of developments within the material-handling robotic market.