Parallel Robots Design: Achieve Ultimate Precision & Speed
What is Parallel Robot Design?
A parallel robots design is a design wherein the arms or links of a robot are simultaneously connected to a base and end-effector. That is, multiple actuators (motors) are utilized to enable parallel movement. The greatest advantage of such a design is that it generates redundant actuation robotics where one actuator may stop yet another can turn on and engage in the same direction of actuation and still get its job done predictably.
Where parallel kinematic machines (PKM) are concerned, some other advantageous features can result from this design. For example, parallel kinematic machines can achieve excellent accuracy, excellent velocity, and excellent stability. This last phenomenon occurs purely for the operation where the inverse kinematics of the robot controls the end-effector positioning.
Key Components in Parallel Robot Design
Kinematic Synthesis Parallel Robots:
Kinematic synthesis is when the optimal configuration of joints, links, and actuators is decided for whatever application. A kinematic model is how one would define where the different pieces of the robot move about one another; thus, in this case, it's significant to understand how best to create that movement.
Degrees of Freedom (DOF):
The necessity of parallel robot construction is the degree of freedom. The higher the degrees of freedom, the better the robot can maneuver to achieve the task; tasks require robotic surgery and delicate machining.
Actuator Placement & Joint Construction:
The initial placement of actuators and construction of joints can establish a robot's efficacy relative to precision and functionality. This requires proper linkage design with actuator positioning to prevent excessive singularity or rigid configurations while operating within a predefined workspace.
Dynamic & Vibration Analysis:
Dynamical analysis modeling of parallel robots determines how loads affect motion and stress on actuators and joints. It improves the efficiency and longevity of the apparatus by determining where maximum stress and vibrations occur.
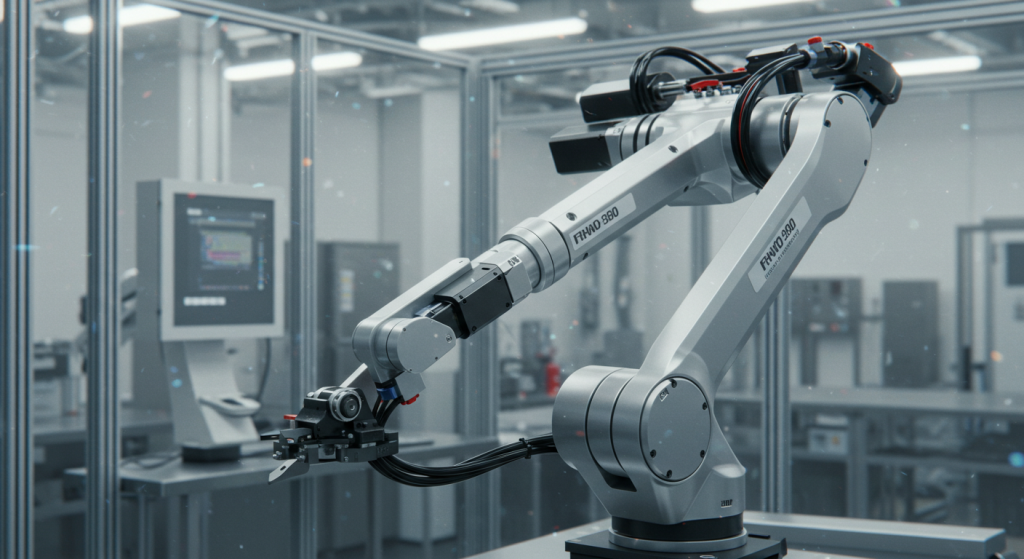
Applications of Parallel Robots
Many industries rely on parallel robots due to their distinct nature. The primary applications of parallel robot construction are:
Manufacturing: For example, in the field of parallel robot design for manufacturing, these robots are utilized for high-speed operations, precision machining, and automated assembly. The capability of doing multiple tasks simultaneously reduces overall cycle times and improves productivity.
3D Printing: For purposes of 3D printing, parallel robot design enables accurate layer-by-layer additive creation of products. These robots allow for higher-quality outcomes and reduced creation times.
Motion Platforms: In regards to motion platforms, robots are utilized for flight and virtual reality simulations. The Stewart platform design is often used in these applications to create efficient and realistic movements.
Mastering Parallel Robot Design: Key Techniques
The ability to appreciate important techniques involved in parallel robot design enables a roboticist to conquer a masterful design of this effective piece of machinery. For example, kinematic synthesis, placement techniques, assessment of joint and actuator placement, and workspace/singularity assessment are paramount to all parallel robot designers.
Kinematic Synthesis in Parallel Robot Design
Kinematic synthesis is the first step in relative manipulator design. The kinematic synthesis allows the robotics designer to see the required joint and limb designs based on anticipated movement characteristics and spaces. Kinematic synthesis prevents the robot from functioning incorrectly with singular issues that impede a parallel robot's success.
Placement Techniques and Assessments of Workspace
Placement techniques for understanding singularity assessment and workspace also help the designer. For example, a workspace singularity assessment is utilized to see if the anticipated end-effector can reach all anticipated points. A singularity assessment prevents certain planes of operation that prevent operation or cause loss of axis control. An excellent designer understands predetermined areas of concern.
Optimization of Performance
The placement techniques of the assessors apply to the joint and actuator placement of the parallel manipulator. Proper placement allows for successful operation with expected movement reliability and outcomes. Excessive placement can lead to mechanical error.
Control and Software Systems of parallel robots
The following are control systems in parallel robot control:
Parallel Robot Trajectory Planning: It creates a feasible trajectory for the end-effector to ensure smooth operation within the intended workspace
• Adaptive Control Parallel Robots: They implement a non-linear system in environments where elements need to change, such as robotic surgeries or tasks that require extreme precision.
• Real-Time Control Parallel Robots: That cannot afford delay, such as assembly lines or systems that require instantaneous input and output.
Materials and Manufacturing of Robot Design
Innovations in materials and the manufacturing process further positively impact the design and assembly of parallel robots. For example, lightweight parallel robot assembly means faster movements and lower energy expenditures, which is crucial for the most demanding aerospace operations. Moreover, the emergence of composite materials and additive manufacturing has become more widely used to create resilient yet lightweight components for the assembly of parallel robots.
Why Warsonco Robotics?
Extensive Experience in Robotics Development
Warsonco Robotics has decades of experience in robotics development. We've integrated over 40 million automation products globally and have expertise in advanced solutions for your automation/project needs. Thus, we can keep your business competitive with updated solutions for your parallel robots.
Capability
Warsonco is a robotics manufacturer specializing in parallel solutions for every industry. Our parallel robots operate at high speed with the precision and flexibility necessary for various applications in manufacturing, medical, and aerospace. They are the experts in kinematic synthesis and robotic system architecture to create reliable, effective systems.
Customized Service
We are your one-stop shop for parallel robots and any automation application. Whether you're looking for a robotic arm or an automated assembly line, Warsonco has a product that can be modified for your application.
Conclusion
The future of parallel robots design is promising, with kinematic modeling contributions, precision control systems, and high-performance actuators all ensuring these machines can operate in tandem with human needs. Everything is trending towards a subcontracted workforce that can do far more than any human error threshold. If your project involves industrial robotics, surgical robotics, or any use where hyper-speed needs are requisite, then parallel robots will solve all of your problems. Visit our blog for more information about parallel robot configurations and what's new in the field.