Parallel Robots Cost Estimation: How to Budget Effectively
What are Parallel Robots?
Parallel robots (also known as parallel manipulators) are multidegree-of-freedom operation systems that use several arms/limbs activated by a collection of actuators and sensors. Unlike serial robots, where each joint added to the overall system complicates movement and potential control, parallel robots cost estimation is simplified. This increased simplicity also increases effectiveness—incredible accuracy, speed, load force, miniaturization, and structural stiffness. Uses include pick and place, machining, medical applications, etc
Why is Cost Estimation Important for Parallel Robots?
Cost estimation for any robotic system is essential for implementation. Understanding from an operational perspective the total cost of ownership (TCO) for parallel robots will better prepare companies for all costs, both up-front and integrative, ongoing additions. When determining whether parallel robot technology is financially sound, one must consider not only the acquisition cost but also the maintenance and integration costs.
Key Components Leading to Cost Estimation of Parallel Robots
Several components contribute to the cost of parallel robots. Here are some of the most prominent:
Actuator Cost
The actuators are the driving force behind a robot's movements, and their cost can vary greatly depending on the type of actuator used (electric, pneumatic, hydraulic). Actuator-cost parallel robots directly impact the performance, efficiency, and precision of the robot.
Materials and Manufacturing Costs
The type of materials used to build (metal, plastic, composite) and the materials costs associated with manufacturing different parts for the actuator cost parallel robots determine the overall cost. From 3D printing the casing to CNC milling parts, the assembly process can get expensive.
Programming Costs
Optional subcomponents must be programmed to ensure usability within the actuator cost parallel robots' physical elements. Regarding cost, time in the development of an extensive programming language dictates pricing for client estimations, as does the inclusion of specific parts.
Research and Development Costs
For actuator cost parallel robots related to new technology, research may need to be done externally to determine better feasibility. These costs are absorbed into the overall cost package, so if you're seeking a quick fix, don't go with it.
Adjustment Costs
Making adjustments to new actuator costs parallel robots will always lead to increased costs due to the personalized evaluations that need to be made in completing the job
Materials/Costs
The materials and costs associated with parallel robots can be expensive. For example, materials such as high-strength alloys and composites make the robot more robust and durable, but the initial cost investment is higher. The cost of materials for parallel robots is based on the application— aerospace, automotive, and medical—requirements.
Software and Design Complexity
Parallel robots usually require specific software to prompt each movement and hone the execution of tasks. The software cost of parallel robots depends on how complicated the software design has to be to complete the required task. Furthermore, the cost of design complexity is associated with how much time and skill it will take to develop a customized solution for your requirements.
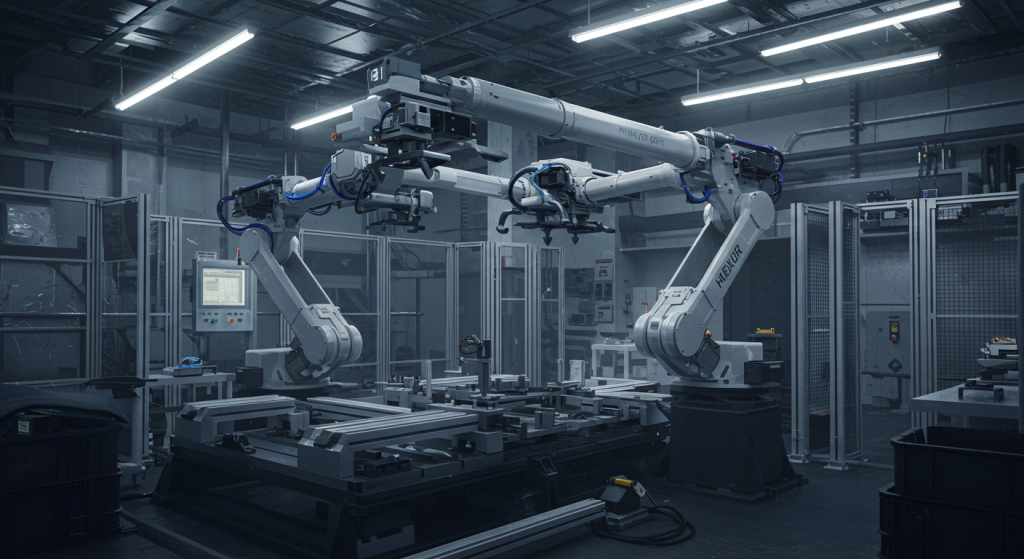
Methods of Estimating Costs for Parallel Robots
Some methods may be used when estimating the costs of robots in parallel:
Parametric Cost Estimation
Using historical analogs or models, parametric cost estimation allows for the estimation of costs to develop a parallel robot based on payload, workspace, and accuracy. This method is quick and provides a relative average, yet it does not always account for all the specific needs of the project.
Bottom-Up Cost Estimation
Employing a bottom-up estimate means that every factor and action (actuator, sensors, integration, etc.) is separately estimated and combined for a total. This method gives an accurate estimate but takes a great deal of time to assess information from every level of need.
Simulation-Based Cost Estimation
Furthermore, with recent trends in the industry geared toward digital twins and simulated tools, the opportunity to use simulation-based cost estimation is more prevalent. This option uses extensive software to simulate the use of the robot during real-world applications, accounting for downtime and maintenance.
Factors to Consider for Later Costs
Beyond the purchasing costs of parallel robots, companies must also consider subsequent operational costs which involve:
Maintenance and Calibration Costs:
The cost of maintenance and calibration of parallel robots is incurred when additional efforts are needed to maintain the functionality of the system during use over time. Maintenance is required to ensure the robot continues to work as it's supposed to; calibration ensures accuracy and decreases downtime.
Operational Costs:
Apparent with the use of the parallel robot, the operational cost of parallel robots is the cost of using the robot for it to do what it has to do: consuming electricity, cooling, and normal wear and tear.
Integration Costs:
The integration cost of parallel robots relates to the costs of combining a new parallel robot into an already existing assembly line. Integration can involve any system tweaks, additional software, and human training needed for proper operation.
Specific Applications Cost Estimations
Specific applications determine parallel robot cost estimations:
Parallel Robot Cost Estimation for Pick and Place Operations:
These need a more precise, more expensive, and faster operation which translates into different parts costs and overall application operating costs.
Medical Parallel Robot Cost Estimation:
Medical parallel robots require additional regulations, higher quality parts, and control systems, thus increasing the overall costs beyond standard expectations. Learn more about where parallel robots could be used in our parallel robot cost estimation post for different industries.
Conclusion
How to Reduce Costs for Parallel Robots Ultimately, parallel robots cost estimation as systems can be reduced through proper evaluation with accurate cost estimation guidance and the reliance upon various assessed factors to make the proper decision for guaranteed effectiveness of parallel robots over time. Also, while parallel robot pricing assessments are available, realistic costs are relative based on use and expected adjustments. Contact today now!