Parallel Robot Kinematics: A Comprehensive Guide
A Comprehensive Guide to Motion, Control, and Applications
Parallel robots—otherwise dubbed parallel manipulators—are multi-articulated systems that utilize multiple arms connected to a singular platform. They are seen across various fields from manufacturing to surgical medical robotics. One specific form of analysis that applies to parallel robots is kinematics, or the study of motion and the absence of forces. For kinematic analysis of parallel robots kinematics, a firm understanding is necessary for control and precision within a manufacturing setting.
What is Parallel Robot Kinematics?
More or less, the kinematics of a parallel robot is the motion analysis of its links, joints, and end-effectors through mathematically determined models specific to each process. Kinematics excludes any force applications and instead focuses on the position, velocity, and acceleration of the above-mentioned parts of the parallel robot.
Delta Robots: High-Speed Precision for Your Production Line
A delta robot, or parallel robot, is one of the fastest, most reliable, and versatile robots available. Delta robots are custom-built for high velocity, low-effort, accurate movements where traditional applications involving linear motion won't operate at the expected speed or demand. For instance, Warsonco Delta Robots feature 60 to 120 cycles per minute and distance traveling up to 1600mm. Thus, it's perfect for assembly lines that require precise repetition and fractional second accuracy since the delta can operate without error or glitching.
Reliable Accuracy and Payload
Delta Robots operate 60 to 120 times per minute with a sustained payload of 3kg, 8kg, and 12kg depending on the application. In other words, they can lift parts, pieces, and packages to 12kg at the same speed of your choosing. From low-weight component assembly to high-weight packaging assembly lines, our Delta Robots can perform all operations seamlessly.
Repeatable Positioning Accuracy of ±0.05mm:
With such accuracy, these Delta Robots are a benefit to any production line as reproducibility and high-quality manufacturing are determined by such detailed specifics. Every movement made by Warsonco Delta Robots is guaranteed via super precise motion control systems—standardization is the name of the game.
Flexible & Large Scale Operation
With travel distances of up to 1600mm, Warsonco Delta Robots can accommodate needs when the distance of operation is necessary. Such operational distances make them applicable in almost all manufacturing situations—whether the environment is large or small, the ability to operate in various locations allows for the setup of production lines to be as efficient as possible.
Quality Manufacturing Solutions
Warsonco is a leader in industrial automation with over 40 million automation solutions installed worldwide. Our Delta Robot will bring about high ROI with revenue generation in about 0.5 to 1 year as they are diverse and exponentially improve production efficiency.
Warsonco Custom Packaging
Each operation, no matter the scale, makes the most of its Delta Robot system. Lifetime Support and Service. Warsonco never compromises on customer service. With a "Service First" support network that runs around the clock, all products receive lifetime support, ensuring Warsonco is an industrial automation partner on which you can rely.
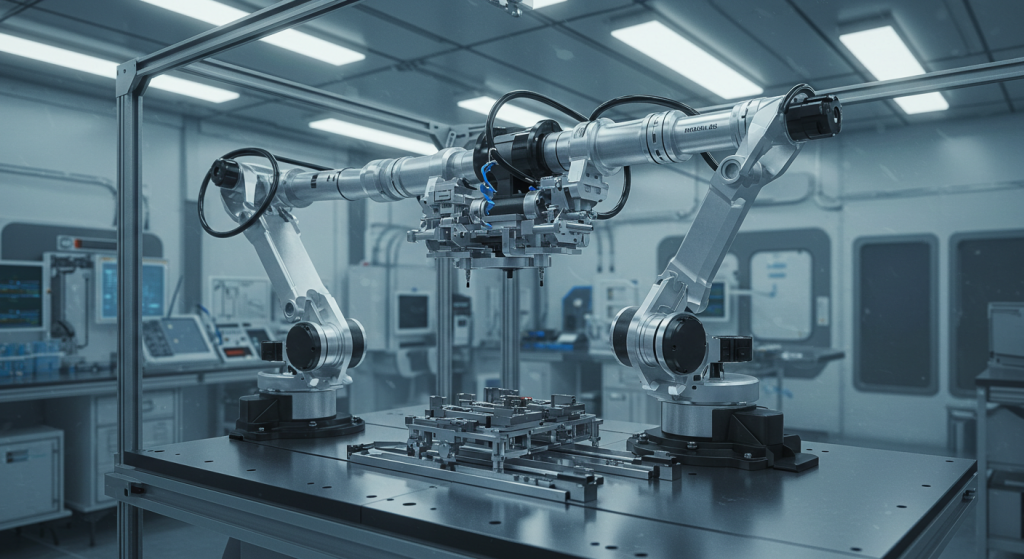
Why Use Warsonco Delta Robots?
Warsonco Delta Robots are perfect for high-performance applications when you need speed, accuracy, and flexibility. If you're looking to reduce errors, improve output efficiency, or automate yet another operation, we have dependable goods and sophisticated solutions for effective production line success over the long term.
Important Terms Relating to Parallel Robot Kinematics
Forward Kinematics:
It's the process of calculating the position and orientation of the end-effector (tool or platform) based on known joint variables (displacements and angles).
Inverse Kinematics:
This is the consideration of joint angles or joint locations needed to achieve a desired end-effector positioning, essentially how to tell a robot how to move.
Kinematic Derivation:
This is the consideration of how to learn and derive the relationship of the various parts of the robot.
Singularity Consideration:
This is important to understand and create potentially disastrous locations where a robot may lose control or degrees of freedom so it does not move inaccurately.
Workspace Consideration:
This is important for assessing the usable space of any given parallel robot, the area where the end-effector can operate, and within where it can be positioned.
Advanced Techniques in Parallel Robot Kinematics
Several advanced techniques and methodologies are used to solve complex kinematic problems in parallel robots.
Numerical and Analytical Methods
Normalized Force is an essential factor when assessing whether a robot will be able to perform desired tasks. Normalized force gives a relative assessment of force exerted across robot platforms.
Repeatability/Variability
The more a robot can repeat certain motions and actions, the more programmable and predictable the output. Assessing the amount of repeatability via deviations from the mean gives an accurate understanding of parallel robots intended for precision.
Orientation/Displacement
Understanding how certain forces can displace a desired orientation is important for assessing whether a robot can have stability in its function. Measuring orientation over time keeps a robot's axis of rotation or a payload in a desired position.
Evaluating Kinematics of Parallel Robots
Recognizing the kinematics of a parallel robot contributes to the evaluation of usability. The characteristics of performance include:
- Accuracy—the ability to get to the intended position
- Precision—the ability to get to the same position consistently, which is great when operations require accuracy consistently
- Repeatability—the access to regain a previously held position from a similar starting point
- Dexterity—the access to which the device can turn and move in different positions
- Velocity and Acceleration Assessment—necessary to understand what can be created by the robot during motion and how quickly it can go.
Applications of Parallel Robot Kinematics
Innovations in parallel robot kinematics can be found in a variety of applications across many fields. These include:
Manufacturing
Wherever there is a need for automation and robotic assembly, parallel robots exist. Its ability to perform precise operations makes it conducive for welding, painting, and material transfer.
Medical robotics
Medical robotics brings about a greater need for the implementation of parallel robots. They possess end effectors that can mimic the exact motions needed for surgery with precision or, subserviently, help with rehabilitation efforts. For example, minimally invasive surgery is an application for a parallel robotic set as it requires the exact and tiny movements parallel robots can specialize in.
Haptic Devices:
The other application of parallel robotics exists within the haptic devices made for virtual reality and teleoperation. These parallel robots control paths of movement while providing feedback so that the user can feel and truly exist in the quasi-existence created for them.
Conclusion
If you're seeking to design, control, or use a parallel robot, you must understand parallel robot kinematics first. Without learning these foundational ideas and mastering them—from forward and inverse kinematics to singularity and workspace analysis—the incredible potential of this superlative robotic system will not be accomplished. Only a few fields in need of acknowledging parallel robot kinematics involve surgical medicine, medical robotics, and more refined automated approaches. Spend time effectively learning the proper groundwork to better your projects and efforts. Where to Learn More. Warsonco Robotics is one of the best places to learn more about all things parallel robots.