Palletizing Robots for Warehouses | Step-by-Step Guide
Introduction to Palletizing Robots for Warehouses
In the rapid evolution landscape of warehouse logistics, Palletizing Robots for Warehouses have emerged as fundamental promoters of efficiency and productivity. The trip of these robots dates back to the first days of automation when manual work was the predominant medium to handle goods. As the demand for faster logistics solutions grew, he also did the need to integrate technology into supply chains. Today, palletizing robots are not simply complementary tools; They are indispensable components of the modern operations of the supply chain, transforming how warehouses work minimizing human error, and increasing the speed and optimization of space.
Types of Palletizing Robots
The diversity in the palette of robots is remarkable. Among the most frequent types are articulated arms, which mimic the movement of a human hand and stand out in complex selection tasks and precision. Palletizing Robots for Warehouses are ideal for handling products in different shapes and sizes, which makes them versatile assets in any environment. In contrast, porch systems offer robust solutions for larger operations that require high performance and wide operational coverage. These systems capitalize on a fixed overload structure, moving along a defined path to stack and organize goods efficiently in palettes. In addition, the emergence of collaborative robots (Cobots) brings a new dimension to warehouse operations, since they are designed to work together with human workers. Cobots improve flexibility and safety in environments where human-robot interaction is crucial, exemplifying a modern approach to shared workspaces.
Components of a Robotic Palletizing System
However, the effectiveness of these robotic systems depends on several essential components. Control systems form the backbone of Palletizing Robots for Warehouses, orchestrating their movements and guaranteeing the precise execution of the tasks. Together with the arm extreme tools, which adapt to the specific products that are handled, these elements work in concert to achieve a perfect operation. In addition, advanced vision systems have revolutionized palletization capabilities by allowing robots to identify, classify, and place elements with precision, regardless of their position or orientation. Such advances are critical to maintaining high-efficiency levels since they minimize the probability of errors and product damage.
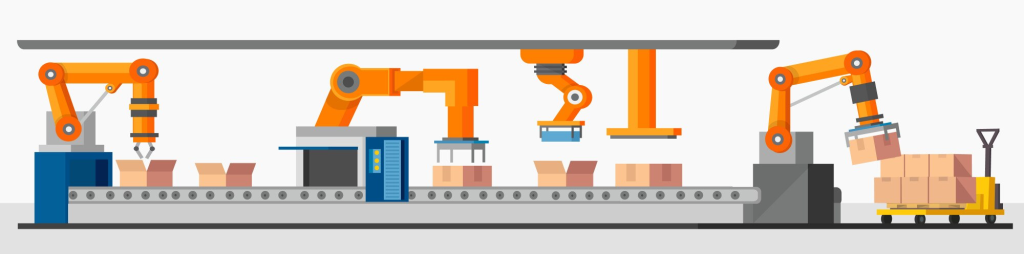
Palletizing and Depalletizing Processes
Recent studies, such as those presented by Aka et al. (2018), underline how technological innovations are further improving palletizing solutions. The introduction of modular systems allows the rapid reconfiguration of robotic configurations to accommodate variable lines of products or demands of change without a time of inactivity or significant expenses. Meanwhile, cable robot technology provides greater flexibility in movement and positioning, facilitating complex tasks in restricted spaces. These advances improve operational efficiency and offer scalability, which is crucial for warehouses that strive to adapt to market fluctuations.
Applications of Palletizing Robots for Warehouses
The remarkable evolution of Palletizing Robots for Warehouses illustrates their important role in the remodeling of logistics efficiency. By taking advantage of a variety of robots, optimizing central components, and adopting avant-garde innovations, stores are equipped to meet the growing pressures of the modern landscape of the supply chain. As industries continue to seek solutions that allow greater agility and response capacity, the adoption of palletizing robots is a strategy with a vision of the essential future to maintain competitiveness in an always dynamic market., The dribble robots have substantially remodeled the processes involved in the storage and recovery operations, introducing a level of efficiency and precision that was previously difficult to achieve. These advanced machines automate the task of stacking the items on the pallets, significantly reducing the costs of time and work associated with traditional manual methods. Using intricate algorithms and vision systems, robot dribbles can identify, orient themselves, and manage various products, which simplifies the entire deposit process.
In different sectors, the applications of dribbling robots are extended. In the food sector and drinks, these robots provide an essential service, efficiently managing products ranging from canned goods to bulk liquids, ensuring compliance with health regulations while improving the throughput. In the same way, in the pharmaceutical industry, where precision is fundamental, robot dribbling plays a fundamental role in management and enclosing precisely, thus minimizing the risk of human error. The e-commerce sector also benefits significantly; While online shopping continues to climb, the warehouses are faced with the dynamic question. The dribble robots allow these operations to climb quickly, and efficiently organizing a wide range of products for rapid recovery and shipping.
Benefits of Implementing Palletizing Robots
The advantages of the implementation of Palletizing Robots for Warehouses are evident in the logistical sector. One of the most convincing benefits is the substantial reduction in labor costs. Automated systems eliminate the need for human workers in repetitive and physically demanding tasks, allowing companies to allocate their workforce more effectively. Furthermore, the greatest safety provided by these robots cannot be overrated; They minimize the risk of injuries in the workplace that can occur with manual dribble, creating a safer environment for all warehouse staff.
Another significant logistical benefit of robotic palletization is the increase in throughput. By optimizing the speed and accuracy of storage and recovery operations, companies experience reduced delivery times, allowing them to meet the needs of customers more sensitively. With the ability to operate continuously, robot dribbles maintain constant productivity, further improving operational agility.
Challenges and Future Trends in Palletizing Robotics
While looking to the future, progress in artificial intelligence and automatic learning will further push the ability to palletize robots for Warehouses. With smarter systems that can learn and adapt to changing conditions, these robots could optimize their operations based on real-time data, improving efficiency and accuracy in ways that we can only start imagining today. In addition, since the logistics industry is preparing for issues related to environmental sustainability, there is a growing impulse to integrate sustainable practices within robotic operations. The dribble robots could play a crucial role in the optimization of the space and use of resources, thus reducing waste and improving general sustainability in warehouse operations.
Conclusion
In essence, the evolution of Palletizing Robots for Warehouses marks a turning point in logistical efficiency, guiding operational improvements in various sectors. Their transformative impact cannot be overrated; While these technologies continue to advance, they are intended to redefine the panorama of warehouse operations, ensuring that companies can not only meet the needs of consumers but thrive in an increasingly competitive market. Shop Warsonco Palletizing Robots for Warehouses and speed up your warehouse work.