Palletizing Robots for Manufacturing in 2025
In the rapid landscape of evolutionary modern manufacturing, the introduction of palletization robots has become a game changer, considerably improving the operational efficiency and the safety of the workplace. These technologically advanced machines automatize not only the repetitive task of palletization but also reduce the risks associated with a manual workforce. The importance of these Palletizing Robots for Manufacturing is based on their ability to optimize the management of the supply chain, reduce labor costs, and improve global productivity, ultimately contributing to a lighter operation that meets market requirements.
Robot Types
Palletizing Robots for Manufacturing are presented in various forms, each specially adapted to meet different manufacturing challenges.
Articulated Robots
The articulated robots, which imitate the amplitude of the movements of a human arm, are incredibly versatile and can manage a multitude of tasks with precision, which makes them ideal for complex palletization applications.
Cartesian Robots
On the other hand, portal robots work with a horizontal aerial design suitable for high-speed and high-volume environments where products must be effectively stacked and organized.
Delta Robots
Collaborative robots, often called cobots, represent another category designed to operate alongside humans. These robots improve security by stretching integrated sensors that allow safe interaction, which makes them ideal for small facilities or processes where human surveillance is critical.
System Components
The effective functioning of Palletizing Robots for Manufacturing depends on their countless components, which work to rationalize the entire palletizing process.
Robot Arm & Controller
At the heart is the robotic arm, designed to perform precise movements and lift heavy objects, thus attenuating physical pressure on human workers.
End-of-Arm Tooling (EOAT)
Improving the arm functionality is the end-of-arm tools (EOAT), which is a customizable grip mechanism that adapts to various forms and sizes of products. This adaptability guarantees that robots can manage different packaging formats without requiring in-depth reconfiguration, thus promoting flexibility in production lines.
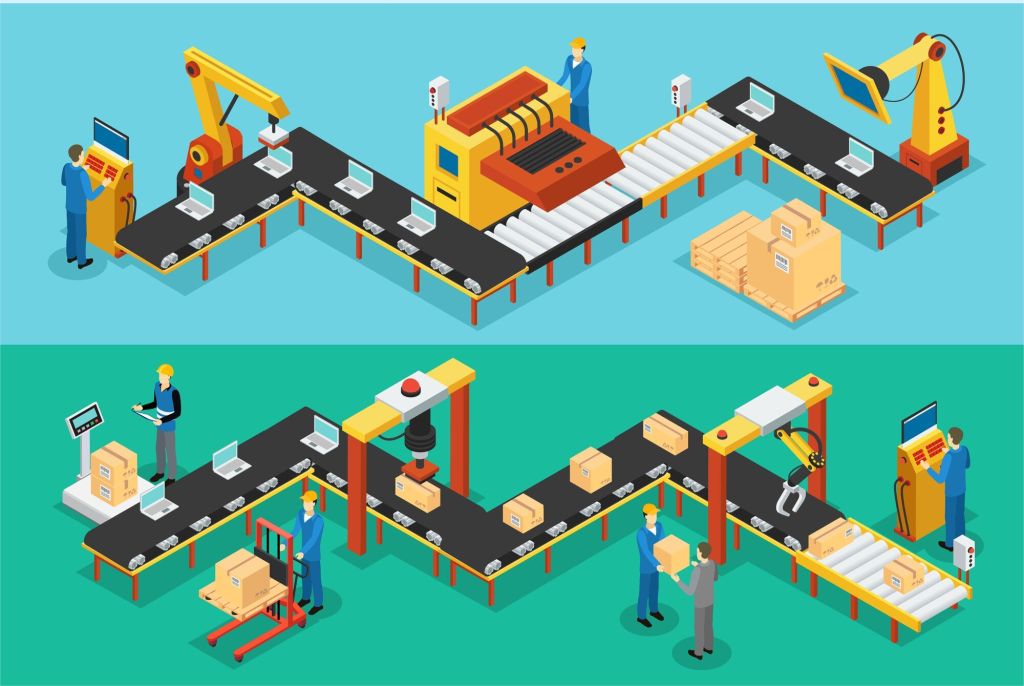
Conveyors (Infeed/Outfeed)
Vision systems are just as important in modern palletization systems, which offer robotic arms the ability to identify and assess the position of the elements. Using sophisticated cameras and sensors, these systems facilitate precise placement and alignment, minimizing error potential. Combined with artificial intelligence algorithms, vision systems allow real-time adjustments, further improving the accuracy and reliability of the palletization process.
Manufacturing Advantages
The interrelation of these components creates a robust palletizing system capable of operating in dynamic manufacturing environments. While robots take care of the most banal tasks but with a high intensity of labor, they release human operators to engage in greater value activities that require critical thinking and creativity. In addition, the deployment of palletization robots improves safety at work by reducing the probability of work injuries associated with heavy lifting and repetitive movements.
Key Manufacturing Benefits
Manufacturers therefore note that investment in Palletizing Robots for Manufacturing is not only to automate a single process but rather to transform the entire fabric of their operations. From the improvement of cycle times to reducing error rates, the advantages extend beyond simple productivity gains and the promotion of a safer and more collaborative work environment. This holistic advantage emphasizes why palletization robots become essential assets in the competitive manufacturing sector today.
Manufacturing Palletizing Processes
The dribble robots are revolutionizing modern production by rationalizing processes and increasing productivity in various sectors. At the center of the palletization efficiency, there is a structured workflow that begins with the robotic system that receives a guide from a production execution system (MES). This integration allows the Palletizing Robots for Manufacturing to precisely identify the items to be managed, evaluate their size, and plan the most efficient stack model for storage conservation. With an optimized workflow, producers can significantly reduce the cycle time between production and storage, effectively increasing productivity.
Case Palletizing
In practical terms, the dribbling process often involves several passages that may include the identification of the articles, the orientation, the harvest, and the formation of the stack. An effective strategy could use a combination of vision systems to ensure accuracy and transport systems for the transport of articles seamlessly. By using algorithms and artificial intelligence, robot palletization can adapt to the variations of the production volume and the size of the packaging, further improving operational flexibility. This adaptability not only maximizes the output but also minimizes the times of inactivity, a critical factor in maintaining a competitive advantage in the frenetic manufacturing panorama.
Conclusion
The transformation facilitated by robot dribbles extends beyond the immediate gains of productivity. I abandon a new era in production in which efficiency goes hand in hand with safety at work. While these robots continue to evolve and integrate with emerging technologies such as the Internet of Things (IoT) and advanced analysis, the potential for further improvements in productivity and safety becomes unlimited. Companies that adopt these higher-level technologies are not just improving their operations; They are preparing the foundations for a future in which production is defined by intelligent automation and resilient systems. SHOP Warsonco Palletizing Robots for Manufacturing and Speed Up Your Manufacturing Tasks.