How Do Parallel Robots Work? A Deep Dive into Kinematics
What are Parallel Robots?
Parallel robots are multi-linked configurations of robotics systems that feature closed-kinematic chains. A serial robot contains joints and links in succession or a chain. A parallel robot has a diverse set of actuators all servicing one end effector within a three-dimensional workspace. Therefore, these types of robotics systems are often used in high-speed and high-precision applications. Any industry in need of meticulous detail and rapid response understands that parallel robotics is the solution. How do parallel robots work? This blog explains the function of robots.
Delta Robot Pick and Place: WSC 1200D with High-Speed Precision Changing Automation
The Delta Robot Pick and Place—WSC 1200D—with High-Speed Precision Changing Automation Technology changes automation technology with high-speed precision for product placement. This Delta Robot operates at a frequency of 60-120 times per minute for effective sorting, packing, and placement. With a quick-moving stroke range of up to 1200mm, it's geared for even the most niche applications at 1200mm WSC. This is a product that fits in line with many other machines/devices and accommodates virtually any industrial operational requirements.
Where is the Application of WSC Delta Robot WSC?
Pharmaceutical Industry
The Daily Chemicals category relies heavily on the Delta Robot Pick and Place to support its continued fast sorting and packing of delicate chemical products that need careful attention to avoid contamination and spoilage. The Delta Robot's precision means that these items get packaged without delay—exposure to air and moisture is reduced—while also decreasing the number of items getting situated incorrectly. Thus, efficiency is boosted with no loss in quality.
Food Industry
The Delta Robot is ideal for the Daily Chemical Industry, where packaging speed and efficiency are needed. It ensures that daily chemical products are packed and sorted at a level of detail that increases production flow and requirements for daily chemical product packaging.
Sorting Hardware
When sorting hardware, the Delta Robot is part of the hardware sorting industry as it effectively and efficiently sorts and packages pieces. Its ability to work with so many different types of products makes it versatile for packaging and sorting needs, increasing efficiency along production lines.
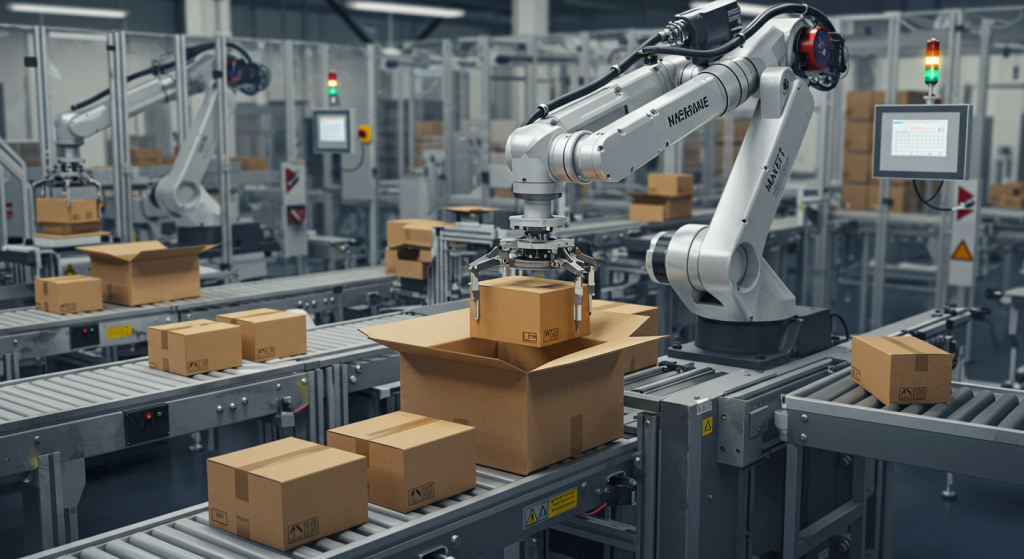
Why Purchase a WSC 1200D Delta Robot?
The cost savings, speed, precision, and high-quality design make the WSC 1200D Delta Robot Pick and Place a required application for any warehouse in need of improved performance through automated assembly. Warsonco premier focus on smart manufacturing places this robot at the top for industrial fabrication, allowing companies to promote automation and speed accuracy on assembly lines.
Major Components and Mechanisms in Parallel Robots
To understand how parallel robots function, it's best to get acquainted with the major components and mechanisms that define them. The necessary parts include:
Actuators (Linear and Rotary)
The actuators are the robot's muscles. A parallel robot's typical motions are achieved through linear or rotary actuators which drive the robotic arms and subsequently the end effector. Therefore, the selection of actuators determines the range of motion and precision of operation.
Linkages and Degrees of Freedom (DOF)
Linkages are the joints and connectors of a parallel robot that allow for movement. Degrees of Freedom (DOF) are the components of independent movement. A parallel robot is generally equipped with 6 DOF which allows for movement in a 3-dimensional space with rotational and translational force.
End Effector
The end effector is the component of the robot that interacts with the outside world. It may be the tool it uses, its gripper, or anything that helps accomplish a specific task. The end effector is what must be maneuvered with the most care to achieve precision assembly, cutting, surgical efforts, etc.
Inverse and Forward Kinematics
Two fundamental terms associated with parallel robot movement are inverse kinematics and forward kinematics. Forward kinematics is determining the joint parameters; inverse kinematics is determining the joint requirements. Inverse kinematics is particularly challenging for parallel robots because they function in closed-loop pathways that require difficult algorithms to solve. Forward kinematics is how the designer/engineer learns potential robot movement to ensure the end effector remains within an appropriate workspace.
How do Parallel Robots Achieve Such Precision in Robotic Positioning?
Parallel robots are known for precise robotic positioning. But how do they achieve such precision?
Kinematic Modeling:
Through kinematic modeling implementations, parallel robots can define and control the positioning of the translational and rotational actuators to create precision. For instance, kinematic modeling is what spatial motion platforms rely upon to ensure every moving part comes together.
Sensor Feedback:
Parallel robots are frequently outfitted with sensors that offer feedback about the actuator's position and movement. Thus, the feedback allows for real-time changes to be made on the fly, increasing accuracy and fixing minute mechanical errors.
Dynamic Modeling:
The dynamics of how the forces produced work against one another are modeled to improve functionality, especially for rapid operation or when a delicate touch is needed, such as with surgical robots or force feedback systems.
Advantages of Parallel Robots
Parallel robots have many benefits over other forms of robots, such as serial or articulated:
• Speed and Efficiency: Since multiple actuators work on the end effector simultaneously in a closed-loop configuration, tasks can be done much faster than with serial robots.
• High Precision: The ability to control movement and the relative actuators creates the opportunity for high precision levels often not found with other types of robotic systems.
• Compact Design: Parallel robots tend to have a smaller footprint, which is beneficial for space-restricted situations.
• Stiffness and Stability: Parallel robots are constructed rigidly, which makes them more stable and less likely to make mechanical errors—even with large or complex loads.
How are Parallel Robots Different from Other Types of Robots?
Parallel robots are different from other types of robots such as serial and SCARA robots. For example:
• Serial Robots: Serial robots have a single chain of joints, which means that the end effector is reliant upon the placement of each joint. This allows for less precision and less flexibility.
• SCARA Robots: SCARA robots have a fixed vertical axis and perform primarily in assembly or packaging. They are fast but do not have the range of motion or precision that parallel robots can have.
• Industrial Robots: Industrial robots have articulated arms and can create or produce anything in a manufacturing capacity, but they lack the speed and precision of parallel robots for some applications.
Conclusion
With applications in everything from robotic surgery to industrial and military robotics to aeronautic and aerospace solutions, parallel robots can be used reliably and with tailored applications. These are the types of robots in which to explore the possibilities, especially with wheels already turning in the kinematic and control sectors. If you'd like to learn more about parallel robots, follow Warsonco Robotics to stay in touch with industry advancements. If you need reliable robots for precise use or custom manufacturable solutions, parallel robots will set your project on the path to a better future.