Overview
Delta Robotics unveils a fast and accurate Pick & Place robot with enhanced features developed to innovate the way production is done. With the speed of operation ranging between 60 to 120 cycles per minute and supporting a travel distance of 600mm, this robot is fitted to do sorting and packing jobs with high velocity and precision. Featuring a triangular body and a state-of-the-art motion control system, Delta Robotics provides an effective answer to industries in need of boosting manufacturing performance for the smart manufacturing era.
The Zhihua series parallel robot embodied in Delta Robotics’ portfolio includes a unique setup of XYZ linear motions and rotational motions around the Z-axis. This design makes the tool ideal for high-speed application, inexpensive, and easy to use hence suitable for several industrial uses.
Technical Specifications /Working Range (mm)
Configuration | |
Settings | Brand |
Servo Motor | Warsonco/Panasonic |
Machine Reducer | Nidec corporation/green |
Controller | Austria KEBA |
Applications:
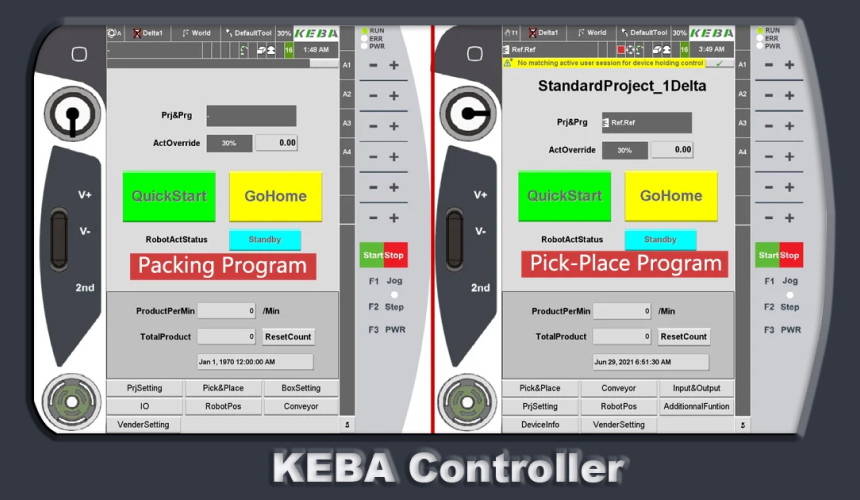
✔ Food Industry: Ensures that the products are properly sorted and packed in a clean manner to meet the required safety standards while at the same time ensuring that time is not a major constrain.
✔ 3C (Computers, Communications, and Consumer Electronics): Ideal for the positioning and enclosures of electronic part, to keep accuracy in these area and minimize handling time in high-tech production.
✔ Daily Chemicals: Responsible for the sorting and packing of daily chemical products in order to have efficient and effective packaging though the company produces high quantities on a daily basis.
✔ Hardware Sorting: Used effectively in sorting and packing of all kinds of hardware and it also proved to have versatility depending on the kind of products that one wants to sort or pack.
Product Features
✔ Accurate Positioning: The robot is aiming to be stable, reliable and flexible to fulfil its task in precise placing of products at each cycle.
✔ Unique Spring Design: Contains a unique spring feature that helps in increasing the lifespan of the robot and at the same time improves on safety.
✔ High Rotation Accuracy: The fourth axis of the robot is capable of a rotational accuracies and repeatability of 0. 05 degrees, which makes it possible to make a specific and exact movement.
✔ Inverted Installation: It is possible to assemble the robot in reverse orientation while it offers good tracking behavior and flexibility to the changes of production lines.
✔ High-Speed Operation: This machine has the capability of performing as many as one hundred and twenty pick-and-place cycles in a minute, thus it is suitable for rush production lines.
✔ Cost-Effective: Provides a good level of performance while coming at a relatively low price, as well as possessing visual dynamic tracking features which improve the usability when operating the equipment.
✔ Strong Performance: This part of the robot design is developed for high bearing capacity; the structure is highly rigid and exhibits great dynamic performance while handling heavyweight loads.
Specifications
Parameters | |||
Model | WSC-600D-L3 | WSC-600D-L8 | WSC-600D-L12 |
Power Rating | four-axis | four-axis | four-axis |
Max Load(kg) | 3kg | 8kg | 12kg |
Standard Cycle Time(s) | 0.4 seconds /cycle (25/305/25 mm) | 0.4 seconds /cycle (25/305/25 mm) | 0.4 seconds /cycle (25/305/25 mm) |
Repeat Positioning Accuracy(mm) | ±0.05mm | ±0.05mm | ±0.05mm |
Angular Positioning Accuracy | 0.05° | 0.05° | 0.05° |
Power | 220V-240v 50/60Hz | 220V-240v 50/60Hz | 220V-240v 50/60Hz |
Power Rating | 2.5kw | 3.5kw | 5kw |
Noise Level | <75db | <75db | <75db |
Protection Level | IP54 | IP54 | IP54 |
Motor Method | AC servo drives | AC servo drives | AC servo drives |
Demonstrator | 7inch demonstrator | 7inch demonstrator | 7inch demonstrator |
Vision Positioning Module | Optional configuration (130W camera, lens, light Source) | Optional configuration (130W camera, lens, light Source) | Optional configuration (130W camera, lens, light Source) |
Operating Instructions | PTP、LINE、PICK、PLACE | PTP、LINE、PICK、PLACE | PTP、LINE、PICK、PLACE |
Installation Method | Inverted | Inverted | Inverted |
Robot Weight | 72kg | 72kg | 72kg |
Playlay load 0.1kg | 0.34s | ||
Playlay load 1kg | 0.38s | ||
Working Temperature | 1-40°C | ||
Humidity Range | 5%~90%(No condensation) | ||
Life Span | 20000 hours+ | ||
GW | 73kg | ||
1-3rd Axis Motor (if) | Panasonic | ||
The Fourth Axis motor(then) | Panasonic | ||
1-3rd Axis Reducer/Gearbox(if) | Harmonic/Nidec | ||
The Fourth Reducer/Gearbox(then) | Leader drive | ||
Controller/PLC | Keba | ||
HMI | Keba |